金属粉末注射成形的工艺研究与应用
陈鸿璋,曾凡同,唐凯,孙同海
精 密 成 形 工 程
金属粉末注射成形(Metal Injection Molding,简称MIM),也 有 资 料 称 为 粉 末 冶 金 注 射 成 形(Powder Injection Molding,简称PIM)技术。它是一种借助塑料产品的成形工艺及装备条件,用金属粉末和粘结剂混合后制成注射粒料在模具型腔中成形,然后经过脱脂、烧结成为金属零件的新型生产工艺.
摘要:介绍了金属粉末注射成形工艺的应用,制备工艺的现状与发展,特别介绍了这项工艺在枪械零件等相关领域的开发与应用。通过对工艺流程的解析,介绍了国外同行生产的同类产品和国内产品的应用。通过应用实例,介绍了国产金属材料采用蜡基材料的可行性,以及采用国内工艺装备实现的工艺过程。
关键词:金属粉末注射成形;成形工艺;应用;热喷涂粉末
1粉末冶金注射成形的内涵与特点
注射成形是将注射粒料在特定的工艺条件下,用注射的方式在模具型腔中成形毛坯零件。粉末冶金工艺及制品的出现将汽车零件的制造尤其是齿轮以极高的速度产业化,使世界的汽车工业向前快速推进。这些都证明了材料工业的发展推进着基础工业的崛起,与之相关的制造工艺也起着至关重要的作用。
和传统的粉末冶金压制工艺不同,金属粉末注射成形工艺的关键是要解决金属粉末的流动性,良好的流动性又是关系到注射零件的性能关键因素。世界一些发达国家,如美国、德国、俄罗斯等国家都在研究和应用具有自己知识产权的注射金属粉末粒料体系,我国目前主要以蜡基体系为主。所谓蜡基体系,就是粘结剂主要成分由蜡组成,配合流动性好又易于脱出的化工材料合成体系,均匀地与金属粉末混合在一起,便于成形毛坯零件,是注射成形工艺的关键环节之一。
金属粉末注射成形的工艺特点:集塑料成形工艺学、高分子化学、粉末冶金工艺学和金属材料学等多学科渗透与交叉合成的工艺技术。利用模具可注射成形毛坯零件并通过脱脂、烧结等工艺过程快速制造出高密度、高精度、三维复杂形状的结构零件;能够快速准确地将设计思想物化为具有一定结构、功能特性的制品,并可直接批量生产出一致性非常高的零件,对枪械零件非常重要。这项工艺技术不仅具有工艺过程少,无切削或少切削,经济效益高等优点,而且克服了传统粉末冶金工艺制品材质不均匀,力学性能低,不易成形薄壁、复杂结构产品的缺点,特别适合于大批量生产小型、复杂以及具有特殊要求的金属零件。
金属注射成形工艺的出现及产业化,解决了在制造领域难以加工结构复杂零件的问题。粘结剂和粘结剂脱出工艺技术的日趋成熟,使得该技术的研究成为现实。可是注射成形本身也存在缺陷,对壁厚超过8mm和零件质量超过200g以上的产品,其内部的粘结剂难以有效脱出,限制了它的使用范围。
正是因为这些限制,注射成形制造的零件通常都是结构复杂,性能及精度要求高,并具有良好的合金化和可再加工热处理的特点。据资料介绍,美国最早研究金属粉末注射成形(MIM)工艺,主要是为了军事领域的需要,重点就是复杂枪械零件的制造。
美国的Indo公司[1]采用金属粉末注 射成形(MIM)工艺生产枪械用零部件(如图1所示)制造枪械。巴西Forjas Taurus S.A.公司[2]用这种工艺制造如图2所示的枪械。
我国采用MIM工艺制造枪械零件起步较晚,2002年才开始开发,2005年开始装备枪械。
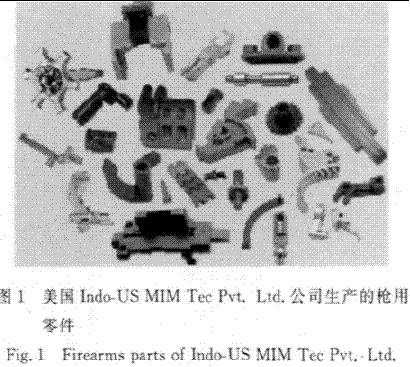 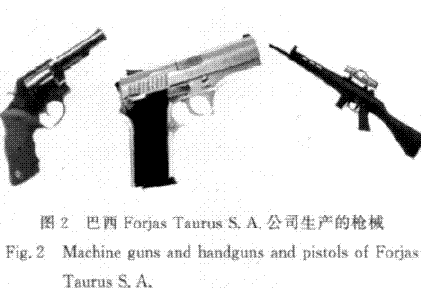
2 粉末冶金注射成形工艺过程与原理
2.1 金属注射成形的工艺流程
金属注射成形工艺流程大体分为:混料、成形、脱脂、烧结和后处理等几个部分,如图3所示。
2.2 工艺流程原理与方法
2.2.1 混料
金属粉末:金属粉末注射成形工艺所用金属粉末颗粒尺寸一般在0.5~20μm之间。从理论上讲,颗粒越细,比表面积越大,越容易成形和烧结。传统的粉末冶金工艺采用的粉末通常粒径大于50μm。金属粉末注射成形制成品密度高,其主要原因是采用了适当粒径的微细颗粒金属粉末。
有机粘结剂:有机粘结剂的作用是粘结金属粉末颗粒,使混合料在注射机料筒中加热成具有一定的流变性和润滑性,也就是说使其成为带动粉末流
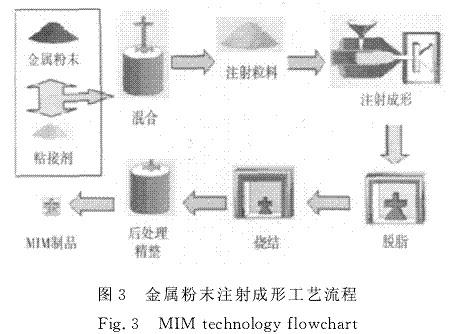
动的载体。由此可见,粘结剂的选择是决定整个粉末成形的载体,是整个粉末注射成形工艺的关键。对有机粘结剂的具体要求如下所述。
1)用较少的粘结剂能使混合料产生较好的流变性;
2)在脱出粘结剂的过程中与金属粉末不起任何化学反应;
3)在制品内不残留粘结剂,产品在烧结后不留碳。
混炼时,将金属粉末与有机粘结剂按照一定的比例均匀地掺混在一起,将其流变性调整到适合注射成形的要求。混合的均匀度对流动性影响很大,它直接影响着注射成形工艺参数的合理选择和成形件密度及其它性能。
为了满足以上要求,首先将合金金属粉末(通常有3种以上的合金材料)均匀混合(物理混合);然后再进行粘结剂和金属粉末的初步混合,在一定的工艺(高温和高速)条件下混合;捏合,使之达到符合工艺要求的均匀“注射粒料”。为保证混合后注射粒料的工艺性,需要对注射粒料的流动性进行检测。
2.2.2 成形
成形过程中,注射粒料在注射机料筒内加热成具有流变性的塑性物料,在适当的压力下注入模具型腔,成形出毛坯零件。生产过程中要严格控制射出温度、模具温度、射出压力等参数,防止出现注射料中各组分的分离和偏析。
生产中要注意毛坯零件的外观,是否有缩孔、裂纹等,一旦出现这些现象应适当调整相关参数。
2.2.3 脱脂
成形零件毛坯在烧结前必须去除毛坯内所含的有机粘结剂。
金属注射成形工艺中的脱脂工艺直接影响最终产品的力学性能,必须严格加以控制。脱脂工艺的设定要根据产品的质量选择相应的工艺方法,如:通常<2g的零件,采取脱脂烧结一体的工艺过程;质量>2g,且壁厚>5mm的零件,采取溶剂脱脂+热脱脂的工艺过程。
溶剂脱脂目前大部分采用溶蜡较好的酒精溶剂。热脱脂的温度通常为400~800℃,国内现在已有比较成熟的电炉装备。
2.2.4 烧结
烧结在通有可控气氛的烧结炉中进行,注射零件的高密度化通过适当的烧结温度和较长的烧结时间完成,从而有效提高和改善零件材料的力学性能。烧结能使多孔的脱脂毛坯收缩致密化,尽管制品的性能与烧结前的许多工艺因素有关,但在许多情况下,烧结工艺对最终制品的金相组织和性能有着很大,甚至决定性的影响。这里要指出的是,注射成形零件的烧结,是在熔与非熔(临界点)的条件下进行的,所以对烧结温度的控制很严格。
2.2.5 后处理
对产品的性能以及内部结构要求较高,尺寸要求较为精密的零件,需要进行必要的热处理、尺寸整形、表面处理等方面的后处理,以改变其性能。这工序与常规金属制品的热处理工序基本相同。
3 金属粉末注射成形的工艺
3.1 标准
与国外金属注射成形工艺技术相比,我国材料工业和装备制造业还处于较低水平,产业化整体评价还处于初始阶段。虽然一些研究机构和企业进行了相应的产业化工作,在开发研究方面做了大量的试验,但还没有系统建立完整的材料体系、试验检测装备和稳定的生产工艺;加上行业和企业之间的“技术壁垒”,还没有形成比较完整的企业标准。目前国家行业归属的管理部门———粉末冶金协会推荐采用美 国MPIF STANDARD 35材 料 标 准 (MaterialsStandards for METAL INJECTION MOLDED PAR-TS)。
3.2 不同加工工艺条件的影响
德国GKN公司的试验情况见表1和表2.由于金属粉末注射成形、粉末冶金和粉末精密锻造加工方法的不同,成本结构有变化,从表2中可以看出其相互区别。注射成形的材料采用超细粉料,是成本增加的主要原因。
金属粉末注射成形工艺具有传统粉末冶金工艺
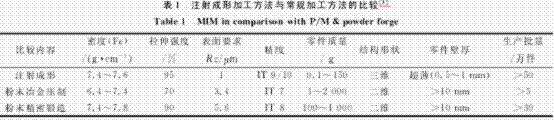 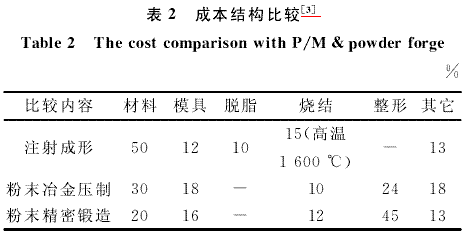
的优点,而形状结构复杂是传统粉末冶金所不能达到的。小型而复杂形状的零件以金属粉末注射工艺最为合适。精密铸、锻造工艺,虽然在近年来其产品的精度和复杂度均得到提高,但仍比不上粉末冶金压制工艺和金属粉末注射成形工艺。粉末锻造得到了重要的发展,已适用于连杆的批量生产。一般而言,粉末锻造的热处理成本和模具的寿命还存在一些问题,仍待进一步解决。
传统机械加工法近些年来靠自动化提升其加工能力,在效果和精度上也有极大的进步,但是基本程序仍然采用切削(如:车削、刨、铣、磨、钻孔、抛光等)完成零件形状的加工。机械加工方法的加工精度远优于其他加工方法,但是其材料的有效利用率低,并且其最后形状的完成受限于设备与刀具,甚至有些零件无法用机械加工完成。相反,金属粉末注射成形可以有效利用材料,不受限制,对于那些批量大且小型、高难度形状的精密零件的制造,金属粉末注射成形工艺与机械加工相比,其成本较低,且效率高,具有很强的竞争力。
我国目前已经采用金属粉末注射成形生产如图4所示的枪械零件。
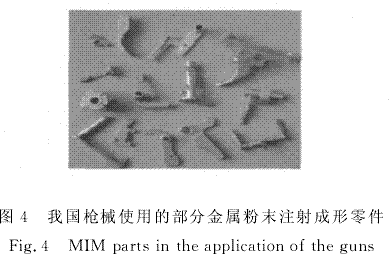
对结构比较复杂的零件,尤其是枪械零件,若采用传统的机械加工方法制造,可以采取先将总体零件分割成容易加工的几个或多个零件,然后再焊接(或其它连接方式)组合成组件;采用金属粉末注射成形技术,可以考虑整合成完整的单一零件,大大减少加工步骤,简化加工程序,不必进行二次加工,或只需少量精加工,零件尺寸公差一般可保持在±(0.05~0.1)mm。
金属粉末注射成形加工工艺对于降低难加工的硬质合金的加工成本,减少贵重金属的加工损失,尤其具有重要意义。采用钨合金材料加工制作的预制破片如图5所示。
注射成形工艺是一种流体成形工艺,由于粘结剂的存在保障了粉末的均匀排布,消除毛坯微观组织的不均匀,使烧结制品密度可达到其理论密度的97%以上。一般情况下压制产品的密度最高只能达到理论密度的85%左右。制品高的致密性可使强度增加,韧性加强,延展性、导电导热性得到改善,磁性能提高。
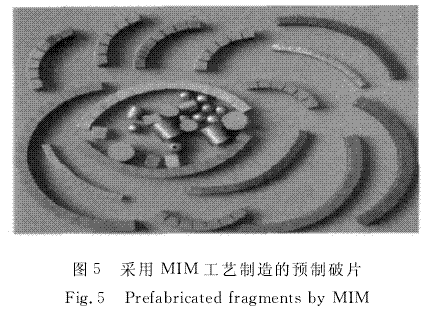
为了实现效率高,大批量和规模化生产,金属粉末注射成形技术使用金属模具,其寿命和工程塑料注射成形模具相当。由于利用注射机成形产品毛坯极大地提高了生产效率,降低了生产成本,而且注射成形产品的一致性、重复性好,从而为大批量和规模化工业生产提供了保证,非常适合于兵器产品的生产。适用材料范围宽,应用领域广泛,如铁基、低合金、高速钢、不锈钢、kavor合金、硬质合金等均可用于注射成形,原则上任何可高温浇结的粉末材料均可由金属粉末注射成形工艺制造成零件,包括传统制造工艺难以加工的材料、高熔点材料。此外,也可以根据用户的要求进行材料配方研究,制造任意组合的合金材料,也可将复合材料成形为零件。
3.3 几种金属注射成形材料的特性
目前国内常用的几种金属注射成形材料的性能参数见表3和表4.
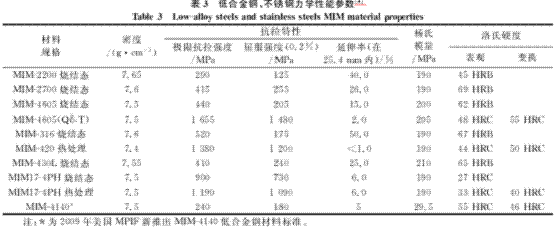 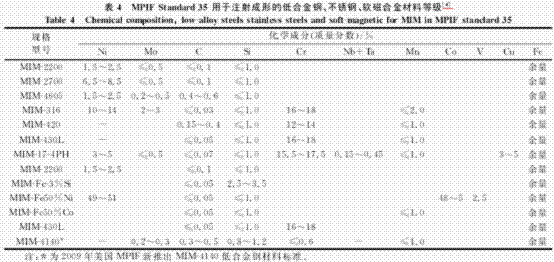
3.4 金属注射成形模具的设计和注意的事项[5]
金属注射成形制品模具的设计原理和塑料模具一样,设计时须考虑诸多因素,如:流道、浇口、型腔、材料等,还要考虑对后续的脱脂、烧结工序的影响。制品的质量与这些因素有直接的关系。模具可以划分为模架和腔体两部分。注射模具模架与塑料注射模具模架完全相同,模架材料可以参考塑料注射模具模架选择。一般动模板、定模板、推板可采用45#钢,调质处理,硬度180~250HBS。其它板料可以采用45#钢或Q235钢。对于精度要求特别高的模架,所有板料均可采用45#钢调质处理,甚至用Cr12类的微变形模具钢,淬火处理。导柱、导套可采用T8A淬硬到50~55HRC或20钢渗碳0.5~0.8mm厚,淬硬到56~60HRC。
注射模具工作时,一般承受20~50 MPa的交变负荷,同时伴有冷热温度交替。在超精密注射成形中,使用的成形压力有时甚至会超过正常使用压力的几倍。注射模具的使用寿命一般为几万甚至几十万次,模具应有足够的强度与刚度。金属注射模具的模腔一般采用硬度为58~62HRC的淬硬模具钢,必须注意由尖角、沟槽、切口及加工缺陷所引起的应力集中。这些缺陷都将显著降低模具的疲劳强度。
对于腔体部分,材料选择主要考虑耐磨性、淬火形状稳定性、耐蚀性及加工性能。由于金属注射材料对模具的冲刷磨损比一般塑料严重,耐磨性好是用于批量生产的金属注射模具腔体的最基本要求,一般要求腔体的硬度在58~62HRC。由于工具钢具有强度、硬度、韧性、淬透性、耐蚀性及加工综合性能好的特点,所以是腔体的首选材料。常用材料有高 合 金 模 具 钢 (如Cr12,Cr12MoV,Cr2Mn2SiWMoV,Cr6WV)及高速钢(如W18CrV,W6Mo5Cr4V2)等。
注射模具一般形状较为复杂,常采用超精密电火花、线切割等电加工手段,要求材料组织均匀,淬透性及淬火形状稳定。金属注射料在注射温度下,常产生腐蚀性气体,耐蚀性好也是对模具材料的一项要求。
总之,模具选择必须综合考虑产品的批量,零件的形状、精度,采用的加工手段及工艺,具备的热处理条件以及材料来源等因素。
金属注射模具一般用于小型零件的生产,模具尺寸很小。正常使用情况下,只要模板的使用尺寸不超过长度和宽度的60%,深度超过10%时,可以不进行强度计算。由于模具形状一般比较复杂,型腔内的实际受力情况也很复杂,即使作出多种假设,也很难用弹性力学及有限元的方法得出结果,因此模具设计常采用放大安全系数的宽容方法。
对于较大制品或采用超高压精密注射成形工艺时,应对型腔的强度进行计算。防止由于强度不足,变形过大产生溢料甚至破坏。较为简单形状模腔的强度计算,可以参考有关塑料模具中设计注射模具的手册。复杂型腔可以采用有限元或专业软件分析计算。为保证制品精度,模具设计应注意以下几点。
1)合理设计模具的放大系数。在保证顺利成形的前提下,尽量减少粘结剂的加入量。
2)合理的模具结构。精密的尺寸部件应有一定硬度,并且更换要方便;采用的公差合理,成形坯“孔”尽量采用公差上限,成形坯“轴”尽量采用公差下限;零件的工艺结构要合理,保证加工精度。
3)合理选择浇口的形式和位置。
4)合理选择顶出方式,尽量使顶出均匀平稳,减少变形。
5)模具应设有温度调节系统。尽量保证均匀填充和冷却,减少密度不均匀。
6)合理选择型腔数量和布局。尽量均匀对称布局,保证平衡填充。特别精密的制品,应尽量减少型腔数目。
7)选择合理间隙,避免产生飞边、毛刺。
4 金属注射成形工艺装备
根据金属注射成形的工艺要求,按照生产模式分主要有2种装备:间歇(批料)式生产、连续式生产。
4.1 混料
金属粉混合,主要采用旋转搅拌混料设备,为了使材料搅拌均匀,采用外旋转与内旋转搅拌的方式。金属粉与粘结剂混合,主要采用高速旋转混料设备,为了使材料搅拌均匀,适当增加温度。捏合混合,为了保证混好的注射材料粒料均匀,须增加一道如图6所示的捏合装备,使注射粒料的均匀一致性更好。
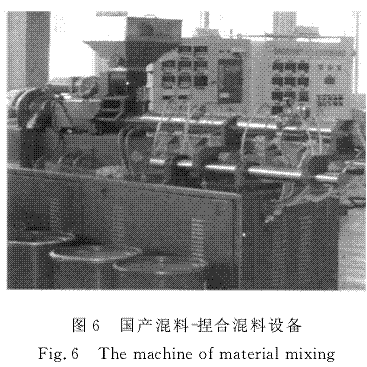
4.2 成形
成形机主要采用注射机,如图7所示。根据注射粒料的特性,必须对注射机进行必要的改造,锁模力要大。
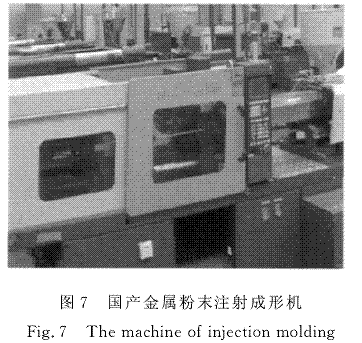
4.3 脱脂
根据不同的粘结剂体系采用不同的脱脂设备。如德国BASF的注射粒料,采取化学催化的工艺方式脱脂,其装备是催化炉。国内一些金属粉末注射成形加工厂多采用独立的催化脱脂设备。德国CREMER公司制造的催化脱脂烧结设备如图8所示。国内比较成熟的就是蜡基粘结剂体系,特点是粘结剂含量比较高,粘结剂脱出的时间比较长,为了保证金属粉末注射成形坯件的强度,采取了“溶剂+热脱脂”的工艺过程。
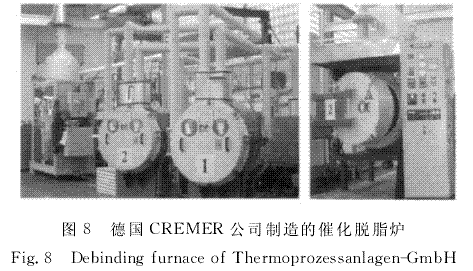
热脱脂装置通常采用气氛烧结和真空烧结2种方式。
4.4 烧结
目前国内使用的烧结设备有提升式烧结炉(如图9所示)、真空烧结炉(如图10所示)、推杆式连续烧结炉和步进梁式连续烧结炉(如图11所示)。
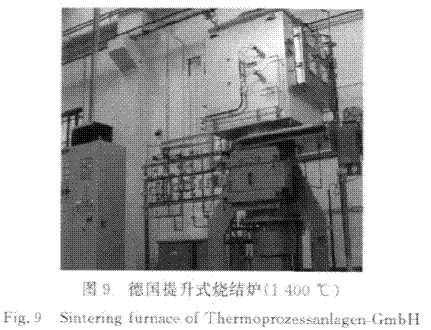 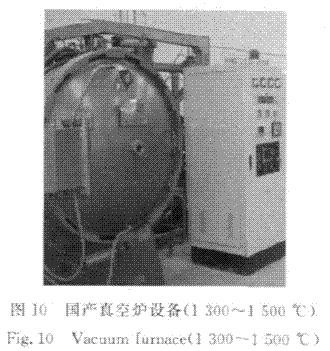
4.5 后处理
对于金属粉末注射成形零件,目前主要是渗碳
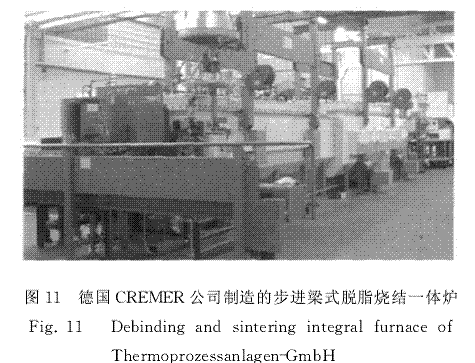
5 金属注射成形技术的发展与展望
从材料来讲,金属注射成形已经具有铁基合金、不锈钢合金、钨基合金、铜基合金等多种材料体系,分别应用于枪械结构零件、引信零件、药型罩、弹头、导弹尾翼、预制破片等领域;采用金属粉末注射成形工艺开发的新枪械产品已取得成功,为枪械零件的生产提供了可靠的技术支持。进一步的开发与研究金属粉末注射成形材料如铜基合金、钛合金、陶瓷等新材料,应用范围将涉及更多的领域。
除此之外,金属粉末注射成形制品在民用产品的应用领域更具有广阔的市场前景[6],如汽车工业:欧洲占到50%以上,北美为14%,日本为17.62%;IT行业:打印机零件、磁芯、撞针轴销、驱动零件等;其中日本为12.31%,北美为22%;北美的枪械占16%。国外电动工具上使用MIM零件如图12所示.
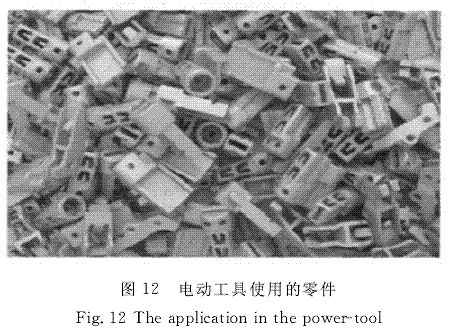
参考文献略
本站文章未经允许不得转载;如欲转载请注明出处,北京桑尧科技开发有限公司网址:http://www.sunspraying.com/
|