Ti-Al球磨粉反应等离子喷涂工艺
吕志军,贺文雄等
中国表面工程
摘要:为制备Ti-Al金属间化合物复合涂层,采用Ti、Al球磨粉在Q235钢表面进行反应等离子喷涂研究,获得了由Al3Ti、TiN、Al2O3、TiAl以及残留Al和Ti组成的复合涂层。虽然球磨可以使Ti-Al混合粉细化与活化,使喷涂时的反应更容易、更充分,但喷涂时Al和Ti仍难以充分反应,且在空气环境中喷涂容易氧化和氮化。涂层与基体之间没有形成冶金结合,而是镶嵌式的机械结合。其结合强度最高值达到了44.75MPa,显微硬度最高值达到了379HV0.5。文中还分析了反应等离子喷涂各工艺参数对涂层组织与性能的影响,并采用正交试验对其在一定范围内进行了优化。得到优化的工艺参数为:喷涂距离为120mm、主气流量为35L/min、喷涂电流为600A、球磨时间为6h。
关键词:机械球磨;反应等离子喷涂;正交试验;复合涂层
0引言
Ti、Al之间发生反应可以得到多种Ti-Al金属间 化 合 物,如TiAl、Ti3Al、Al3Ti等。其 中TiAl以其密度低、高温强度大,以及抗蠕变、抗氧化性能好等优越性能而被认为是极具应用潜力的新型结构材料,在航空航天、汽车制造等领域具有十分广阔的应用前景;Ti3Al的强度和硬度很高,常作为增强相;Al3Ti的抗高温氧化性能好。但这些Ti-Al金属间化合物都很脆,如TiAl的室温脆性大,难以加工成型,使其大规模应用受到了很大的限制[1]。而采用热喷涂方法在材料表面形成含有Ti-Al金属间化合物的复合涂层,以改善材料的性能,也是一种可取的应用途径。研究人员已对此进行了一些尝试,有采用TiAl预合金粉等离子喷涂制备TiAl合金涂层[2-3],也有采用Ti、Al单质粉末等离子喷涂制备Ti-Al金属间化合物涂层[4],还有采用Ti、Al球磨粉进行喷涂并研究喷涂时的反应和喷涂产物[5-7]。此外,对Ti-Al金属间化合物涂层的性能也有一定的研究[8,9]。
反应热喷涂技术由自蔓延高温合成(SHS)技术与热喷涂相结合发展而成,其采用高放热反应体系材料为喷涂材料,利用传统喷涂热源熔化并引燃喷涂材料的SHS反应,在喷涂的过程中同时完成材料的合成与沉积,用于制备金属陶瓷涂层并取得突破。与传统热喷涂相比,反应热喷涂具有两大优势:一是涂层制备成本较低;二是涂层致密,结合强度高[10-13]。机械球磨可以细化Ti、Al粉末,增加粉末的表面能和晶格畸变能,从而使粉末活化,加快反应速度,使反应进行得更充分。文中采用Ti、Al混合粉的机械球磨和反应等离子喷涂方法在Q235钢表面制备涂层,并对喷涂工艺参数进行了优化。
1 试验方法
选用的Ti粉纯度为99.4%、粒度为48μm,Al粉纯度≥99.0%、粒度为75μm,两者按原子数分数1∶1进行混合。首先采用QM-2SP(16)型行星式球磨机对粉体进行机械球磨,球磨时的球料比是10∶1;同时加入相当于粉末质量3%的甲醇作为过程控制剂,以防止粉体球磨过程中粘结在磨球和罐壁上。球磨前先将罐内抽真空再充Ar气进行保护,球磨机转速为300r/min。球磨后采用APS-2000A型等离子喷涂设备进行喷涂。基体材料选择Q235钢板,尺寸为76mm×54mm×1.2mm;喷涂前对基体表面进行超声波清洗、喷砂处理。喷涂主气为氩气,在空气环境中进行,送粉速度为20g/min。采用正交法选取其他主要试验参数。试验选取正交表L9(34),试样编号为B1~B9,选择涂层与基体的结合 强度 (y1)和 涂层的显 微硬度(y2)为考核指标。4因素的水平安排具体见表1,正交试验参数如表2所示。
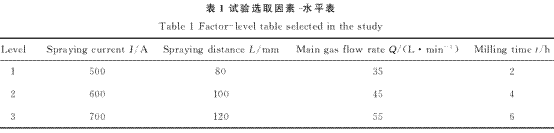 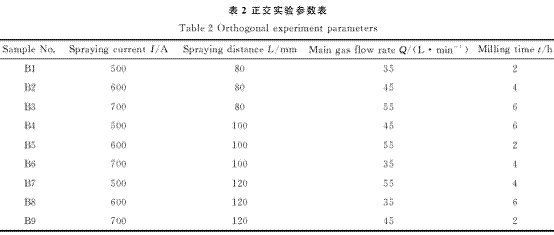
用ZRY-2P型综合热分析仪对球磨前后的Ti、Al混合粉进行差热分析。采用XD-2型X射线衍射仪(Cu靶Kα射线)进行物相分析,扫描速度为4°/min。用粘结剂对偶试样拉伸试验法测定涂层与基体的结合强度,根据国家标准GB/T8642-2002制作拉伸试样,粘结剂采用E-7树脂胶。使用CSS-44100型电子万能试验机进行拉伸试验,加载速度为6mm/min。显微硬度测试在HVS-1000型数显显微硬度计上进行,所加载荷为500g,加载时间为15s,在垂直于基体表面的方向上依次取5个点测量,以平均值作为涂层的显微硬度值。
2 试验结果与讨论
2.1 Ti、Al混合粉球磨前后的差热分析
图1是未球磨与球磨不同时间的Ti、Al混合粉的差热分析曲线。图中未球磨的Ti、Al混合粉在300℃左右出现了一个平滑的放热峰,是由于粉末表面被空气缓慢氧化放出热量导致,在大约640 ℃左右,又出现放热峰,是由于Al、Ti固相下相互扩散形成Al3Ti金属间化合物引起;在660℃时,体系出现了吸热峰,这时温度达到了Al的熔点,使Al熔化所致,在770℃左右,出现了一个放热峰,归结于熔化的Al发生强烈反应:Al+Ti+Al3Ti→TiAl,从而形成放热峰。
图1中球磨4h与球磨6h的差热分析曲线基本一致,但与未球磨的Ti、Al混合粉的差热分析曲线明显不同。球磨4h与球磨6h的Ti-Al复合粉的差热分析曲线分别在282 ℃、283 ℃对应于较尖锐的放热峰,这是由于粉末表面被空气较剧烈的氧化放热所致。可见,球磨使粉末活化,以致易于被氧化。两曲 线 分 别 在606 ℃、602℃对应于第二个放热峰,是由于Al、Ti固相下相互扩散形成Al3Ti引起。随着球磨时间的延长,形成Al3Ti的放热峰变强、峰值对应温度下降,说明球磨导致粉末中积蓄的能量增加,加速了低温下Ti、Al原子相互扩散速率,降低了形成Al3Ti的激活能;同时,球磨使Ti、Al层片间距减小,缩短了原子扩散距离。两曲线在665 ℃时对应的吸热峰为接近Al熔点时所发生的Al熔化吸热现象;之后由于系统的温度持续升高,熔化Al的扩散能力极大的提高,两曲线分别在771℃、772℃时为放热峰,是由于熔化的Al发生强烈反应:Al+Ti+Al3Ti→TiAl,形成了一条强放热峰。两曲线都在871 ℃对应于最后一个放热峰,是因为系统中残余的Ti与生成的Al3Ti和TiAl等的反应:Ti+Al3Ti+TiAl→Ti3Al+TiAl,以及亚稳态金属间化合物向稳态转变放热所致。曲线最后两个放热峰的强度下降,是因此前的氧化反应以及形成Al3Ti的反应中消耗了大量的Al,致使后面的反应受限所致。
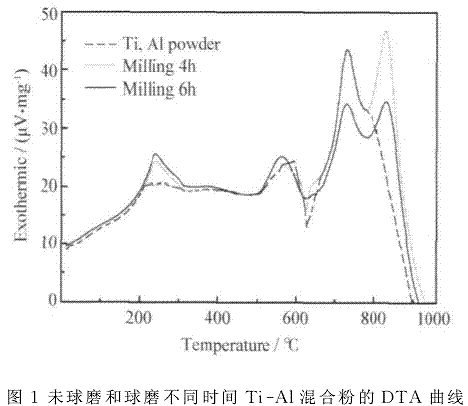
比较图1中各曲线,可以看出,球磨使Ti-Al粉末的氧化温度降低,氧化更剧烈,而且发生反应Al+Ti→Al3Ti所需的温度也降低。由此可见,球磨起到了活化粉体的作用,使粉末更容易发生化学反应。
2.2 涂层的成分与组织分析
图2是喷涂试样的X射线衍射图谱。由图中可以看出,Ti-Al球磨粉在空气环境中反应等离子喷涂所得涂层的成分非常复杂,不同工艺参数喷涂所得涂层的成分也有所不同,但都包含Al3Ti、TiN、Al2O3,都残留尚未完全反应的Al和Ti,其中B2、B3、B4、B6、B7涂层中含有少量TiAl,B4、B5、B7涂层中含有少量Ti3Al。由于Ti、Al相互反应生成金属间化合物的反应不充分,且生成物并非平衡产物,因此所得涂层并非单纯的Ti-Al金属间化合物涂层,而是一种包含多种成分的复合涂层。涂层中之所以产生TiN和Al2O3,是因为喷涂在空气环境中进行,很难避免空气的侵入,而作为活泼金属的Ti和Al在空气侵入时很容易发生氮化和氧化。具体而言,在高温下Ti极易与N发生反应生成TiN,而Al则极易氧化生成Al2O3,且生成的Al2O3致密,覆盖在Al颗粒表面会阻碍反应的进一步进行,从而导致Al的残留。但所得TiN和Al2O3作为性能稳定的硬质相,能改善涂层的耐磨损、耐高温性能。
Al和Ti的残留,除了上述原因外,还由于粉末颗粒在等离子喷涂时的高速飞行和快速冷却,以致在高温下停留时间非常短,即便经过球磨的活化处理,喷涂时仍难以充分反应。
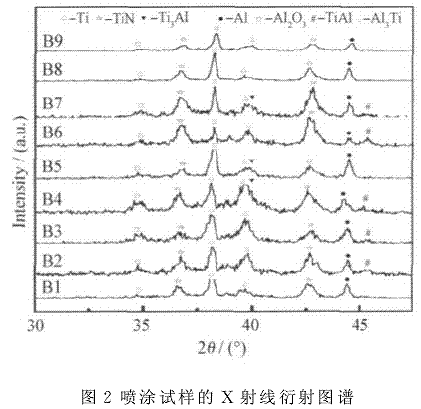
图3是涂层的组织图片。从图3(a)中可以看出,涂层由多种相组成,是一种复合涂层,且各相分布不够均匀。同时可以看出,涂层中无明显孔洞和裂纹等缺陷的存在,涂层与基体界面无明显过渡层存在,表明没有发生冶金结合,而是一种镶嵌式的机械结合,但总体上结合良好。从图3(b)中的线扫描结果也可以看出,涂层中除了含Ti和Al两种元素以外,还存在N和O元素,进一步证实喷涂时发生了氧化和氮化反应。同时,由于Ti和Al两种元素分布不够均匀,进一步证明涂层中各相分布不够均匀。
2.3 涂层的性能及影响因素分析
表3是喷涂试样的正交试验结果与极差分析。从表3中可以看出,涂层与基体的结合强度比较高,最高值达到了44.75MPa;大多数涂层的显微硬度均高于基体,最高值达到了379HV0.5。从表3中还可以看出,4个因素对涂层与基体结合强度的影响从高到低依次为:喷涂距离(L)>主气流量(Q)>喷涂电流(I)>球磨时间(t),优化参数为L3Q1I2t2,即:喷 涂距离为120 mm、主气流量 为35L/min、喷涂电流为600A、球磨时间为4h。4个因素对涂层显微硬度的影响从高到低依次为:主气流量(Q)>球磨时间(t)>喷涂距离(L)>喷涂电流(I),优化参数为Q1t3L3I2,即:主气流量为35L/min、球磨时间为6h、喷涂距离为120mm、喷涂电流为600A。
图4是不同水平的因素对涂层与基体结合强度以及涂层显微硬度的影响。
(1)喷涂电流的影响结合强度与显微硬度随电流的增加均呈先增加后减小的趋势。电压不变时,电流增加功率会加大,进而使粉末颗粒的加热温度升高,有利于粉末颗粒的熔化和充分反应,使结合强度与显微硬度提高。但电流过高时,热输入太大,使涂层的组织粗大,冷却后涂层中的残余应力大,容易变形开裂,以致结合强与显微硬度降低。实验结果表明,喷涂电流600A为最佳。
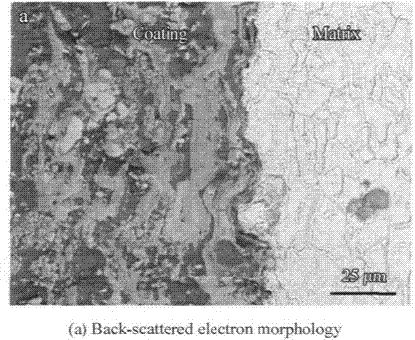 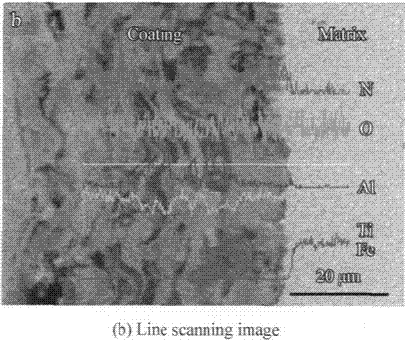
(2)喷涂距离的影响
随喷涂距离的增加,结合强度呈现递增趋势,显微硬度则是先减小后增加。喷涂距离较小时,粉末颗粒在等离子焰中停留的时间较短,在到达基体前颗粒的温度较低,没有达到充分熔化和反应,形成的涂层不够致密。当L由100mm增加至120mm时,粉末颗粒在电弧中停留时间更长,加热温度更高,反应更充分,到达基体表面时,形成更致密的涂层,结合强度更高。
(3)主气流量的影响
结合强度与显微硬度随主气流量的增加均呈递减趋势。氩气流 量 直 接 影 响 等 离 子 焰 的 热 焓 和 速率[14],进而影响喷涂粉末颗粒到达基体瞬间的温度和速率。随着氩气流量的增加,喷涂时粉末颗粒的温度会下降,因为需要加热的气流量增加;而喷涂时粉末颗粒的速率会随之提高。主气流量为35L/min时,粉末颗粒的熔化状况达到了最佳;当主气流量继续增加时,喷涂时粉末颗粒的速度过高,缩短了粉末颗粒在等离子焰中的“滞留”时间,使粉末颗粒加热与反应效果降低,涂层的硬度及其与基体的结合强度都降低。
(4)球磨时间的影响
结合强度随球磨时间的增加呈先增后减趋势,显微硬度呈现逐渐增加的趋势。球磨4h的粉体较球磨2h粉体有所细化,喷涂时反应更充分,硬质相含量增加,因而结合强度与硬度提高。随球磨时间的进一步增加,粉体得到了进一步的细化与活化,喷涂时反应更充分,硬质相含量进一步增加。当硬质相含量超过一定数值,虽然其硬度继续提高,但其与基体的结合强度将会下降。从另一方面看,球磨时间的延长加大了粉体的细化,使其表面积增大,也加剧了与卷进来的空气反应而造成氧化与氮化。
Galvanetto E等[15]对喷涂层中的氮含量与显微硬度的关系进行研究表明:涂层的显微硬度值随着涂层中氮含量的增加而单调递增,而与基体的结合强度则降低。当球磨时间从4h增加到6h,结合强度虽然降低,但其降低的幅度小于显微硬度提高的幅度,因此球磨6h的涂层的综合性能更好。
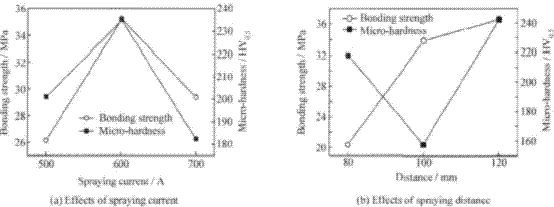 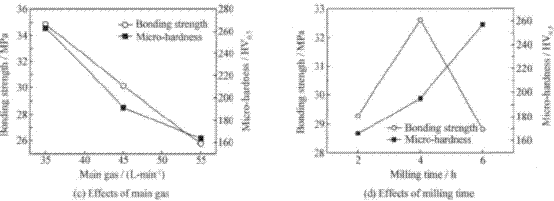
3 结论
(1)机械球磨可以使Ti-Al混合粉细化与活化,使等离子喷涂时的反应更容易、更充分。(2)制备的含有Ti-Al金属间化合物的复合涂层其成分主要是Al3Ti、TiN、Al2O3、TiAl,以及残留的Al和Ti。说明喷涂时Al和Ti仍难以充分反应,且在空气环境中喷涂容易氧化和氮化。(3)涂层中各相分布不够均匀,但无明显缺陷。涂层与基体之间没有形成冶金结合,而是镶嵌式的 机 械 结 合。其 结 合 强 度 最 高 值 达 到 了44.75MPa,显微硬度最高值达到了379HV0.5。(4)正交实验获得的球磨与等离子喷涂对涂层结合强度和硬度的影响,其最优工艺参数为:喷涂距离为120mm、主气流量为35L/min、喷涂电流为600A、球磨时间为6h。
参考文献略
本站文章未经允许不得转载;如欲转载请注明出处,北京桑尧科技开发有限公司网址:http://www.sunspraying.com/
|