高压氢还原制备钴包球形碳化钨的工艺研究
侯玉柏, 鲍君峰, 崔 颖
热 喷 涂 技 术2012 年 9 月
摘 要: 钴包碳化钨粉是一种用于等离子、爆炸喷涂工艺的复合型粉末材料,广泛应用于航天、航空和冶金等部门的特殊环境下。本文采用高压氢还原的湿法冶金工艺制备了高质量钴包碳化钨粉末。 讨论了不同工艺参数如催化剂、试验温度、硫酸铵、氨水及氧分压等,对碳化钨粉末的钴包覆质量的影响。 探究发现,最初的敏化和活化处理非常重要。 通过大量实验结果得到制备包覆完整的球形碳化钨 / 钴颗粒合适的工艺参数。
关键词: 氢还原;碳化钨;等离子;热喷涂
碳化钨 / 钴热喷涂粉末的特性往往因其制粉工艺方法的不同而异[1]。 通常的制备方法有烧结破碎法、团聚烧结法、混合法、包覆法、熔融法等[2]。 有些方法易造成混合不匀,从而制约涂层的性能。 为了获得致密、显微结构均匀的材料,已经发现用包覆的方法可以提高粘结金属的混合均匀程度,改进涂层材料的显微结构,从而提高性能的稳定性[3]。碳化钨 / 钴涂层的耐磨性能主要来自于碳化钨, 但在喷涂过程中瞬时高热 ( 温度超过 800℃)时,碳化钨极易分解脱碳,脱碳的程度与颗粒总表面有关[4]。 根据 Bobrov 用等离子喷涂碳化钨时,粒度与失碳量的关系为:90~150μm 时,失碳 17%;40 ~90μm 时 失 碳 48.5% ;<40μm 则 失 碳 为59.8%[5]。 中国科学院上海硅酸盐研究所采用等离子喷涂纯碳化钨粉末 ( 粒度 <40μm, 化学组分:W93.9%;C6.1%) 时得到的涂层的化学组分是:W96.95%;C 3.05%, 涂层中碳的脱失量与 Bobrov 的结果相近[6]。
钴包碳化钨是以碳化钨为核心,在它的周围均匀地包覆一层金属钴的包覆粉末。它的主要特点是在喷涂加热过程中防止碳化钨中碳的损失,在基体表面上制得具有较高硬度和良好耐磨性能的钨钴硬质合金涂层[7-8]。
1 实验原理
从金属盐的水溶液中用氢气还原金属是一种经典的湿法冶金方法。钴包碳化钨包覆粉末是采用液相加压氢还原工艺制备的[9],即:碳化钨粉末悬浮在含钴溶液中,在高压氢的作用下,使溶液中钴离子在碳化钨粉末活性表面进行还原, 形成金属钴层,将碳化钨颗粒牢固地包裹在内。 该过程的基本反应式为:Co(NH3)nSO4+H2+WC Co/WC+(NH4)2SO4+(n-2)NH3(n≥2) (1)
2 实验方法
2.1 原料与设备
实验主要原料为 2000℃条件下制备的球形碳化钨粉末。 其它的实验药品主要是:硫酸铵( 工业纯),氨水( 工业纯),硫酸钴( 化学纯),去污剂,腐蚀剂,敏化剂,活化剂,催化剂。 实验设备是带有磁力搅拌器的 2L 高压釜。釜内设有蛇形冷却水管,热电偶套管,三叶螺旋桨式搅拌器,釜底部是电加热装置。
2.2 实验过程
最初的实验是将 WC 颗粒直接加入到高压釜中,结果发现包覆效果不好,如图 1 所示。原因是碳化后,没有进行粉末表面任何预处理,碳化钨表面缺少形核的活化点,钴与碳化钨没有亲和力,所以必须对碳化钨进行净化、粗化、亲水化处理。其流程为:在去污剂溶液中煮沸→漂清→腐蚀剂溶液中煮沸→漂清→用敏化剂溶液进行敏化→最后用活化剂溶液活化。去污剂处理可除去碳化钨表面上的有机物和油污,腐蚀剂的强氧化性可使碳化钨表面受轻微侵蚀而达到微观粗化的目的。敏化和活化主要是为了让钴在碳化钨表面快速沉积, 得到均匀、致密的包覆层。
反应溶液的配制:在不锈钢容器中按比例加入硫酸铵( 工业纯),氨水( 工业纯),硫酸钴( 化学纯)和水,在搅拌加热的条件下溶解,直到所有颗粒溶解。
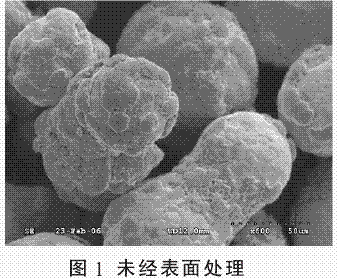
将配制好的溶液先加入高压釜中,溶液不应超过釜容积的 2/3, 然后将经过表面预处理的碳化钨粉与催化剂一并装入釜内,盖严密封。 升温至要求范围,控温充氢到一定气压,反应至氢气压力不变结束,卸釜排料,液固分离,洗涤烘干,分析检测。
3 实验结果与讨论
制备钴包覆粉末的诱导期一般为 10~30 分钟,反应时间是 40~80 分钟。 如果反应时间过快,钴与 WC 结合不好,游离钴粉太多;反应时间过长,钴将在碳化钨表面某些易成核点集中成核,造成包覆不均。 根据现场生产经验,反应时间控制在 45~60 分钟较为合适,而诱导期越短越好。 下面分析诱导期和反应时间与一些影响因素的关系。
3.1 催化剂的影响
催化剂起着活化氢与传递氢的作用,即生成的OH- 吸附在碳化钨表面形成活化点,Co2+ 首先在这些活化点上发生还原,成核并逐渐长大,因此活化点的多少直接影响反应过程和包覆情况。图 2 为催化剂用量对还原过程的实验结果,当用量小于 0.2g/L 时,诱导期随活性剂的加入明显缩短;当用量大于 0.2g/L 时,诱导期受活性剂的影响很小。 在用量小于 0.1g/L 时,反应时间随催化剂的加入明显缩短;用量大于 0.1g/L 时,对反应时间影响很小。 最终选择催化剂用量是 0.2g/L。
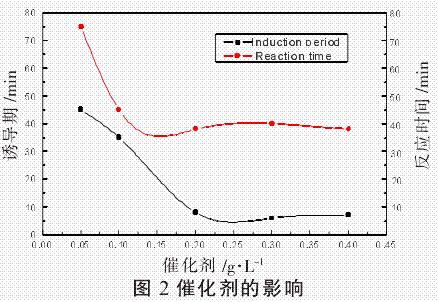
3.2 温度的影响
温度对反应过程的影响很大,其对诱导期及反应时间的影响见图 3。 由图可见,随着温度的增加诱导期明显降低,在 160℃以后,趋势平缓,160℃是一个临界状态。 随着温度的升高反应速度加快,反应时间明显缩短。 低于 150℃时,反应时间很长,需要一个小时以上,即使反应到氢分压不变,出料后溶液也没有完全反应, 颜色依然很深。 高于150℃时,随着温度的升高,反应时间进一步缩短,到了 170℃以后, 反应时间减小的趋势变小。 在170℃左右,反应到氢气分压不变后,出料时溶液接近无色,说明反应已经较为完全。 在 190℃以上进
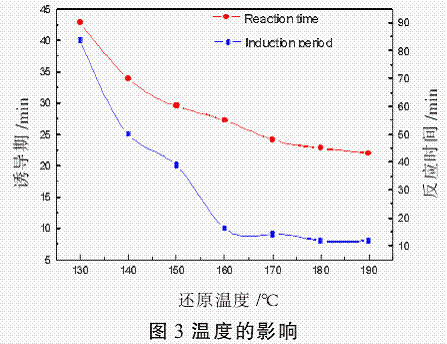
行反应,诱导期和反应时间均缩短,但是由于反应太快,钴粉独立形核,最后形成与碳化钨粒度相近的钴颗粒。 如图 4 所示。
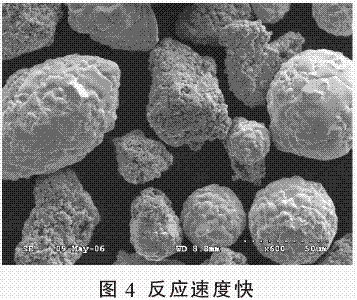
最后选择在 150℃时通入氢气, 关掉加热器,在 160℃时经过一段诱导期后,反应开始。 针对反应时间合适范围,温度应维持在 160~170℃之间。
3.3 硫酸铵的影响
反应体系中,硫酸铵起着很重要的作用,首先它提供与 Co2+ 形成 Co(NH3)n2+所需的氨,第二是使体系变成一个缓冲溶液, 在该 pH 范围内不会产生氢氧化物或碱式盐沉淀,第三是过多的加入硫酸铵,会使反应向不利于生成金属钴的方向进行,同时减少氢气在溶液中的溶解度,从而使反应速度变慢,因此可以利用硫酸铵的加入量来调节反应速度。
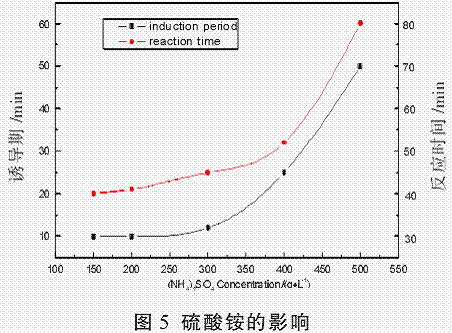
硫酸铵对反应过程的影响见图 5 ,其浓度明显制约着还原速度。 随着硫酸铵浓度的增加,诱导期和反应时间明显延长。 硫酸铵对还原速度的影响,可从反应方程式 (1) 获得理论依据, 在反应式中(NH4)2SO4是生成物,根据反应平衡移动原理,当其量较少时,平衡向正反应方向移动的趋势大,因此还原速度较快。 当其量缓慢增加时,逆反应的趋势逐渐增强,导致正反应减缓,即还原速度减慢。 最后选择硫酸铵加入量范围为:300~350g/L。
3.4 氨水的影响
由基本反应方程式可看出,加入氨水的作用有两个,一是为了与钴离子络合,形成钴氨络离子,避免形成钴的沉淀物;另外与硫酸铵共同形成缓冲溶液,中和还原过程中所生成的 H+稳定体系 pH 值。Co(NH3)n2+中的 n 可以从 1 到 6 ,在反应体系中除加入的氨水外, 还加入硫酸铵, 也提供了一定量的氨。图 6 为氨水浓度对反应过程的影响,反应的诱导期随氨水加入量的增加而延长,反应时间也延长,当氨钴摩尔比等于 5 时,在 60 分钟内未见反应。 最后选择氨水与钴的摩尔比是 2.5:1。
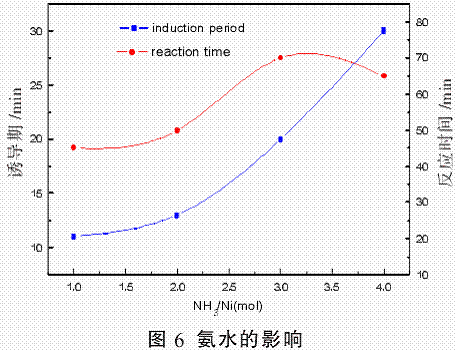
3.5 氢分压的影响
氢气是反应体系中的还原剂,是非常重要的反应参数, 其在液相中的溶解度受诸多因素影响,而氢分压是重要的影响因素之一,其对还原过程的影响见图 7,随着氢分压的升高,诱导期变短,反应时间也缩短。 这是因为氢分压升高时,其在溶液中的溶解度增加,换句话说,是反应物浓度增加,反应速度自然加快。 反应不是越快越好,同时氢气压力受设备限制, 根据反应情况, 氢分压最后定为 2~4MPa。
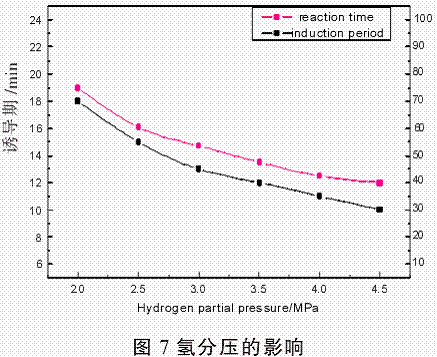
3.6 钴包碳化钨形貌观察
经过对影响包覆情况各因素的分析,选择一定的参数进行了包覆试验。 钴含量不同,其包覆后形貌也有差异,如图 8 所示。 从图 8b 中可以看出,钴含量为 17.21%包覆情况十分理想, 保留了原始WC 粉的球形度,包覆层也很致密均匀。 图 8c 钴含量 12.07%的包覆层也比较均匀致密。图 8d 钴含量7.62%,因为钴含量较少,包覆层不能连续,有部分WC 表面裸露出来。 为了进一步观察包覆层,做了钴含量 17.21%单个球形粉末剖面的面扫描, 如图9 所示。 从图中可以看出,钴与碳化钨结合紧密,包覆层连续而致密。
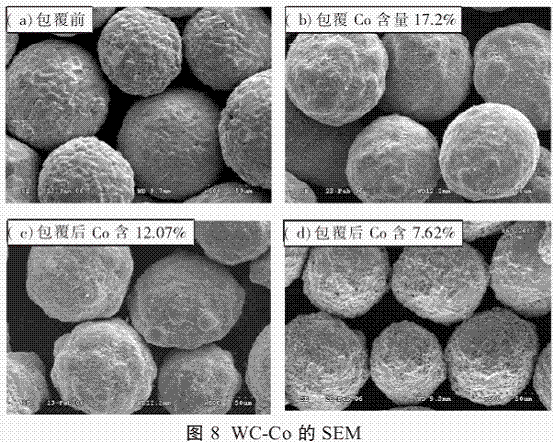 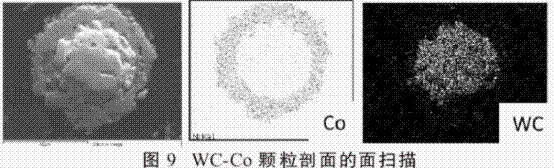
4 结论
本文讨论了采用液相加压氢还原工艺参数对制备钴包碳化钨粉末质量的影响。研究结果表明最初的敏化和活化处理非常重要。处理不好直接影响反应和包覆情况,还会使游离钴粉大量增多。 同时通过大量的试验,讨论分析了影响包覆反应的部分因素,合适的工艺参数是:催化剂量为:0.2g/L;反应温度:160~170℃;硫铵加入量:350g/L;氨水与钴的摩尔比为:2.5:1;搅拌强度为 1000r/min,反应时间控制在 45~60 分钟, 可以制得包覆完整的球形碳化钨 / 钴颗粒。
参考文献略
本站文章未经允许不得转载;如欲转载请注明出处,北京桑尧科技开发有限公司网址:http://www.sunspraying.com/
|