近几十年,许多研究小组利用阳极氧化、粘结固体润滑膜、磁控溅射、喷涂法、激光熔覆等方法在钛合金表面制备含有润滑物质的自润滑涂层来达到改善其摩擦磨损性能的目的. 但这些方法一般存在工艺复杂或者处理过程中的高温易降低膜层和基底性能等缺点。微弧氧化技术是一种电化学表面处理工艺,能够在钛基底上微弧放电生成一层陶瓷质氧化物涂层,相比于以上技术具有操作工艺简单,氧化膜与基体结合牢固,高的硬度,良好的耐蚀和耐高温冲击性,适用于工业化生产等优点。但是,利用微弧氧化的方法制备的陶瓷涂层往往具有较高的摩擦系数. 过高的摩擦系数不仅易造成涂层自身的磨损失效,而且会加剧对偶材料的磨损。因此,为了进一步提高微弧氧化陶瓷涂层的摩擦磨损性能,必须降低其摩擦系数。一种有效的方法是制备含有固体润滑物质的自润滑微弧氧化陶瓷涂层.而目前研究含润滑物质的自润滑涂层,多采用两步法。为了进一步提高钛合金表面微弧氧化陶瓷涂层的摩擦磨损性能,在石墨分散的Na2CO3-Na2SiO3-KOH电解液溶液中一步制备了含自润滑微粒的微弧氧化复合涂层。利用X 射线衍射仪(XRD) 、X射线光电子能谱仪(XPS) 和扫描电子显微镜(SEM)研究了未添加和添加石墨微弧氧化涂层的相组成和微结构,采用往复式球-盘试验机评价了两种涂层的摩擦学性能. 结果表明: 加入到电解液中的石墨在微弧氧化过程中进入到涂层中,从而得到含有固体润滑微粒的复合涂层; 在干摩擦条件下,含石墨的微弧氧化涂层相比于不含石墨的涂层具有更小的摩擦系数。
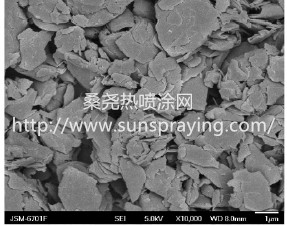
本文由桑尧热喷涂网收集整理。本站文章未经允许不得转载;如欲转载请注明出处,北京桑尧科技开发有限公司网址:http://www.sunspraying.com/
|