纳米碳化钨增强镍基合金热喷涂涂层的摩擦磨损性能研究
姚舜晖,苏演良,高文显,郑凯文
摩擦学学报
摘要:采用高速氧焰喷涂技术制备质量分数为40%纳米碳化钨增强镍基合金涂层,探讨其显微组织、相组成及硬度,并评价其摩擦磨损性能.结果表明,与传统碳化钨增强镍基合金涂层相比较,两类涂层的组成相同,但纳米碳化钨增强镍基合金涂层组织中的碳化钨颗粒尺寸较小且分布更均匀,其硬度比传统碳化钨增强镍基合金涂层高10%,磨痕深度小20%.
关键词:高速氧焰喷涂;纳米碳化钨;镍基合金涂层;摩擦磨损性能;热喷涂
高速氧焰喷涂技术(High velocity oxygen-fuel spray, HVOF)赋予熔融粒子以高动能,所形成的热喷涂涂层致密度高,广泛用于抗磨和耐腐蚀工具用涂层.镍基合金普遍用于高温氧化、腐蚀及耐磨环境[1],而碳化钨/钴金属陶瓷(WC/Co cermet)兼具高硬度和高韧性的优点,广泛用于苛刻工业环境中的抗磨材料[2~5].引入碳化钨硬质相可以进一步提高镍基合金的抗磨性能[6, 7].近来针对纳米尺度(Nano-scale)材料的研究结果显示,纳米材料的某些性质远优于传统材料,国内许多学者亦积极开展了纳米涂层材料的应用研究[8, 9],并开发出多种制备纳米涂层的方法[10, 11].人们在纳米结构碳化钨研究中发现,纳米碳化钨的硬度和抗磨性能优于传统(微米)碳化钨[6, 7, 12~15].
本文作者将纳米碳化钨作为增强相引入镍基合金中,采用高速氧焰热喷涂技术制备出纳米碳化钨增强镍基合金涂层,探讨了涂层的组织结构、硬度和摩擦磨损性能;同时与采用相同技术制备的传统碳化钨增强镍基合金涂层进行对比分析,以期为进一步了解纳米碳化钨与传统碳化钨的性能差异及其在喷涂和制造工业中的应用提供实验依据.
1 实验部分
制备涂层所用原材料为喷涂专用粉末,基材选用镍基自熔合金粉末,增强相为纳米碳化钨粉末,其成分及物理性能见表1和表2.采用电子天平(精度

0.1 mg)按质量分数(全文同)40%与60%秤取纳米碳化钨和镍基合金粉末,充分混合后用于制备热喷涂涂层.基材表面经清洗、喷砂粗化、预热处理后,采用SulzerMetcoDiamond Jet(DJ) 2700型喷涂系统,以丙烯为燃气、氧气为助燃气制备热喷涂涂层.主要工艺参数见表3.制备出的涂层经研磨、抛光至表面粗糙度Ra在0. 1μm左右,以下简称Hn.另一对照组为传统(微米)碳化钨增强镍基合金热喷涂涂层,

采用传统碳化钨作为增强相,其基本性能见表2,相应的镍基合金粉末基材亦为镍基自熔合金粉末,碳
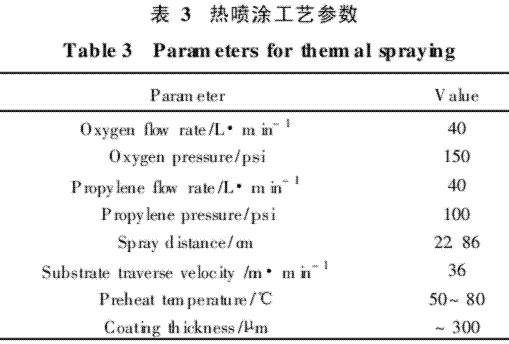
化钨含量同样为40%,制备出的涂层以下简称Hc.采用X射线衍射仪(XRD)分析涂层的晶体结构和相组织;采用扫描电子显微镜(SEM)观察涂层的显微结构;采用Vickers型显微硬度计测量涂层的显微硬度(载荷1. 96 N,硬度值为涂层横截面随机测量16点的平均值);采用表面轮廓仪测量涂层的表面粗糙度及磨痕深度(depth ofwear scar);采用德国制SRV型往复式摩擦磨损试验机评价喷涂涂层的摩擦磨损性能[16].摩擦副接触方式为球-盘点接触,圆盘[材质为JIS S31C钢,其组成为: 0. 31% C,0. 27% S,i 0. 55%Mn, 0. 03% P, 0. 035% S,余量Fe;其表面涂覆热喷涂涂层]以夹具固定不动,而偶件试球[材质为AISI52100钢,其组成为: 1. 39%Cr,1. 03%C, 0. 22% S,i 0. 31%Mn, 0. 01% P, 0. 01% S,0. 06%Cu, 0. 07%N,i余量Fe]受正压力作用紧贴于圆盘表面.试球直径为10 mm,圆盘直径为24 mm,厚度为7. 9 mm.利用置于圆盘下部夹具中的压电动力计测得电压值,传至计算机并经转换计算出摩擦系数,其精确度可达小数点后5位.摩擦磨损试验条件为:干摩擦条件下,载荷15 N,滑动振幅0. 5 mm,频率30Hz,时间15 min.
2 结果与讨论
图1所示为传统和纳米碳化钨/钴喷涂粉末形貌的SEM照片.由图1(b)可见,传统碳化钨/钴粉末颗粒中穿插有孔洞,其晶粒尺寸为0. 5~2. 5μm;经EDXA成分分析结果表明,各单一粉末颗粒由微米碳化钨、钴金属及介质充分混合后烧结而成,为团聚-烧结型粉末.图1(c)为纳米碳化钨/钴粉末形貌的SEM照片,图1(d)为图1(c)粉末的纵剖面显微组织形貌照片.对图1(d)进行EDXA成分分析,结果显示单一纳米碳化钨/钴粉末颗粒以纳米碳化钨为主,以金属钴粘结重新造粒而成,其晶粒尺寸介于50~500 nm.
图2所示为喷涂原料粉末的XRD图谱.可见,镍基合金粉末(图2中曲线a)主要由Ni组成,同时含有Ni3B、Cr7C3、Cr3C2和CrB析出相,而Fe和Si因含量太低无法检出.与此同时,纳米和传统碳化钨粉末(图2中曲线b和曲线c)的相组成相同,皆由WC和Co相组成.
图3所示为碳化钨增强镍基合金涂层的XRD图谱,图中曲线a为传统碳化钨增强镍基合金涂层(Hc),曲线b为纳米碳化钨增强镍基合金涂层(Hn).可见,Hc和Hn的相组成相同,主要由基底镍合金以及所添加的碳化钨增强相构成,此外还含有碳化铬和硼化铬(Cr7C3、Cr3C2和CrB)析出强化相.对比图3与图2中曲线a可以看出,经过喷涂加热过程后,部分镍合金中的析出强化相呈非晶化趋势.
图4所示为传统(Hc)和纳米(Hn)碳化钨增强镍基合金热喷涂涂层的纵剖面显微组织形貌SEM照片,其中图4(a)为Hc涂层的横截面组织形貌照片,图4(b)为图4(a)的局部放大图;图4(c)为Hn涂层的横截面组织形貌照片,图4(d)为图4(c)的局部放大图.由图4(a和c)可以看出,涂层具有镍基合金和碳化钨交互堆积的层状结构,为高速氧焰热喷涂涂层的一般结构.对比可知,Hn中的碳化钨[图4(c)]在镍基合金基底中的分布较在Hc中均匀[图4(a)].由图4(b和d)可见,涂层基底由饱和镍固溶相和Ni-Ni3B共晶相组成,基底中散布碳化铬和硼化铬析出物,白色块状物则为碳化钨.从相应的放大照片来看,Hn中的碳化钨尺寸[图4(d)]远
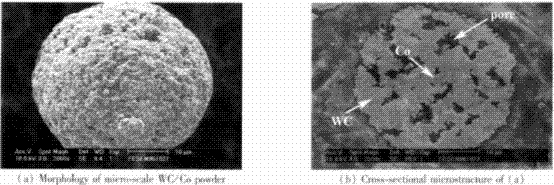 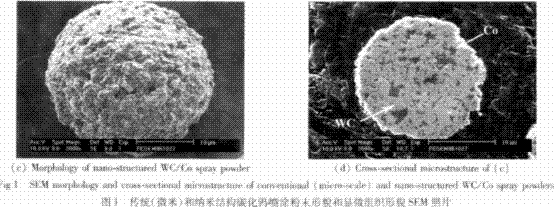
比Hc中的碳化钨[见图4(b)]要小且分布更加
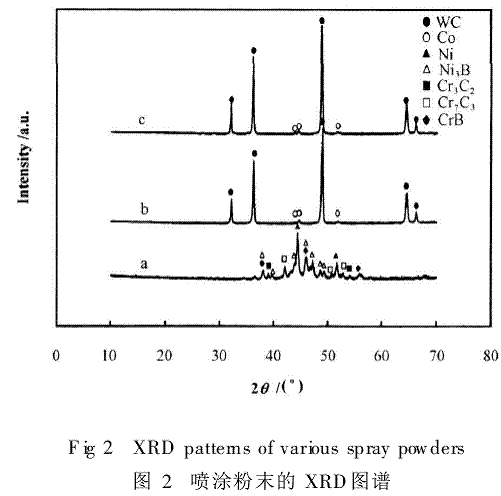
均匀.
表4示出了2种涂层的硬度及摩擦磨损试验结果.可以看出,Hn涂层的硬度较Hc高约10%.与此同时,Hn涂层的磨痕深度比Hc小约20%,其摩擦系数亦相对较低.总体而言,与传统碳化钨增强镍基合金涂层相比,纳米碳化钨增强镍基合金涂层的硬度较高,抗磨性能较好,表明采用纳米碳化钨取代传统碳化钨作为增强相的效果是正面的.图5示出了纳米碳化钨增强镍基合金(Hn)涂层磨损表面形貌SEM照片.可见涂层磨损表面存在一层粘附物质,经成分分析得知其含大量铁和氧;铁
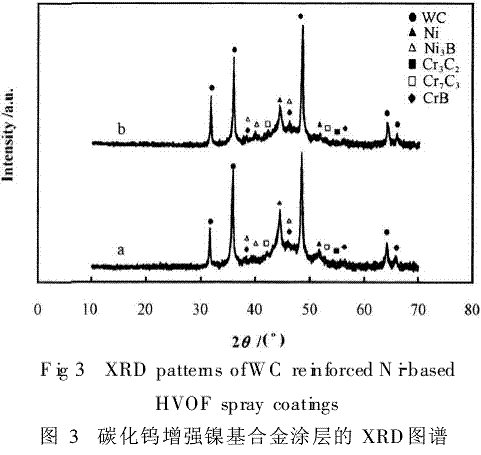
和氧的原子比(a.t% )约为1∶2,显示该粘附层可能为各种氧化铁(FeO、Fe2O3、Fe3O4等)的混合物.与此同时,粘附层中心局部区域可见暴露的底材,显示涂层在摩擦磨损过程中发生粘附和剥落交替作
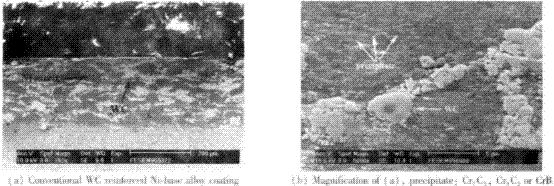 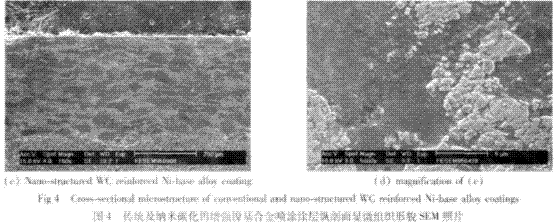  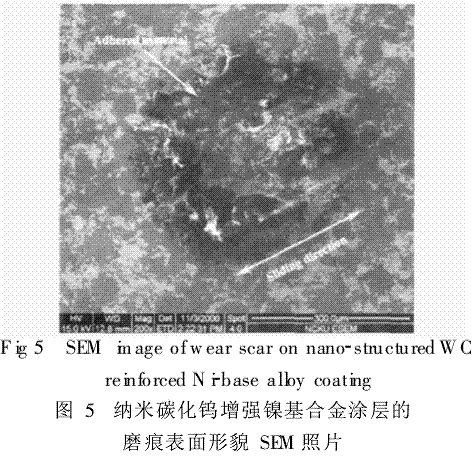
用,涂层因而产生磨损,且涂层磨损源于粘着和氧化磨损.传统碳化钨增强镍基合金涂层的摩擦磨损机制与纳米碳化钨增强镍基合金(Hn)涂层相似.综上所述,纳米碳化钨和传统碳化钨除了组成(化学成分)相同外,其它如制造方法、颗粒尺寸和结构等皆不同. Stewart等[17~19]指出,纳米碳化钨因尺寸小、比表面大,在喷涂加热过程中常产生严重脱碳,并生成W2C、W、η(CoxWyCz)等结晶相,这些硬脆相的产生对机械性能和抗磨性能非常不利.值得注意的是,如图3所示,采用本研究选定的操作参数所制备的涂层并未发生上述脱碳现象.而对比图4和图5可知,纳米碳化钨均匀分布于镍基合金基底中,有利于减小合金基底的位错滑移平均自由路径,阻碍和限制位错滑移,从而使其硬度提高,抗磨性能改善[13, 20];而粘附和氧化磨损所导致的破坏也因涂层整体硬度的增加而降低.因此,通过谨慎选择喷涂参数可以避免脱碳现象的发生,从而更好地发挥纳米碳化钨对镍基合金涂层的增强作用.
3 结论
a. 以选定的热喷涂参数可以制备出抗磨性能良好的纳米碳化钨增强镍基合金涂层,其在喷涂加热过程中不发生脱碳现象,纳米碳化钨在镍基合金基底中的分布较均匀,粒度较小.
b. 引入纳米碳化钨增强相可以有效地提高镍基合金涂层的硬度和抗磨性能,从而拓宽其工程应用范围.
参考文献:
[1] Fern′andez E, CadenasM, Gonz′alez R,et al. Wear behavior of laser clad NiCrBSi coating[J]. Wear, 2005, 259: 870-875.
[2] deVilliersLovelockH L, Richter PW, Benson JM,et al. Pa-rameter study ofHP/HVOF depositedWC-Co coatings[J]. Jour-nal ofThermalSprayTechnology, 1998, 7: 97-107.
[3] AkasawatA K. Wear properties ofWC-Co coatings prepared with plasma and high velocity oxygen fuel spraying[C]. In: Proceed-ings of the 15th International Thermal Spray Conference, Nice,France, 1998. 281-286.
[4] HawthorneHM,ArsenaultB, Immarigeon JP,etal. Comparison of slurry and dry erosion behavior of some HVOF thermal sprayed coatings[J]. Wear, 1999, 225-229: 825-830.
[5] KarimiA,Verdon C,Martin J L,et al. Slurry erosion behavior of thermally sprayedWC-M coatings[J]. Wear, 1995, 186-187: 480-486.
[6] Jia K, FischerT E. Sliding wear of conventional and nano-struc-tured cemented carbides[J]. Wear, 1997, 203-204: 310-318.
[7] Jia K, Fischer T E. Abrasion resistance of nano-structured and conventional cemented carbides[J]. Wear, 1996, 200: 206-214.
[8] 关耀辉,徐杨,郑仲瑜,等.等离子喷涂纳米FeS涂层的摩擦磨损性能研究[J].摩擦学学报, 2006, 26 (4): 34-38.
Guan Y H, Xu Y, Zheng Z Y,et al. Tribological properties of nanostructured iron sulfide coating deposited by plasma spraying[J]. Tribology, 2006, 26(4): 34-38.
[9] 赵晓琴,周惠娣,陈建敏.等离子喷涂纳米和常规喂料WC-Co涂层在干摩擦和水环境中的摩擦磨损性能研究[J].摩擦学学报, 2006, 26(3): 18-23.
[10] 王群,丁彰雄,陈振华,等.超音速火焰喷涂微米和纳米结构WC-12Co涂层及其性能[J].机械工程材料, 2007(4): 21-24.
[11] 栗卓新,王江萍,蒋建敏,等.纳米涂层的几种制备方法[J].机械工程材料, 2004(1): 31-33.
[12] 王宇栋,王飚.WC-M纳米复合涂层的制备方法及其组织、性能[J].纳米科技, 2006(3): 51-56.
[13] KearB H,McCandlish L E. Chemical processing and properties ofnano-structured WC-Comaterials[J]. Nano-structuralMateri-als, 1993, 3: 19-30.
[14] McCandlish L E,Kear B H,Kim B K,et al. Low pressure plas-ma-sprayed coatings ofnanophaseWC-Co[M]. In: YaziciR M(Ed. ), Protective coatings: Processing and characterization,The Minerals, Metals and Materials Society,Warrendale, PA, 1990.113-119.
[15] GellM. Applying nanostructured materials to future gas turbine engines[J]. Journal ofMetals, 1994, 46: 30-34.
[16] Yao SH, SuY L,KaoW H,etal. Evaluation onwearbehavior ofCr-Ag-N and Cr-W-N PVD nanocomposite coatings using two different types of tribometer[J]. Surface and CoatingsTechnolo-gy, 2006, 201: 2 520-2 526.
[17] StewartD A, Shipway P H,McCartney D G. Abrasive wear be-havior of conventional and nanocompositeHVOF-sprayedWC-Co coatings[J]. Wear, 1999, 225-229: 789-704.
[18] de Villiers LovelockH L. Powder/processing/structure relation-ships inWC-Co thermal spray coatings: A review of the published literature[J]. JournalThermal Spray Technology, 1998, 7: 357-373.
[19] He Jianhong, Schoenung Julie M. A review on nanostructured WC-Co coatings[ J]. Surface and Coatings Technology, 2002,157: 72-79.
[20] Armstrong R W. The influence of polycrystalline grain size on mechanical properties[M]. In Herman H (Ed. ), Advances in materials research, Interscience Publishers, New York, 1970.101-108.
本站文章未经允许不得转载;如欲转载请注明出处,北京桑尧科技开发有限公司网址:http://www.sunspraying.com/
|