电热爆炸喷涂的发展及其关键技术分析
魏世丞, 徐滨士,王海斗,金 国
中国表面工程
摘 要:电热爆炸喷涂是一种新型的表面工程技术,可用于零件内孔以及外表面的耐磨、防腐涂层的制备。电热爆炸喷涂反应可形成冶金结合层,同时涂层为微晶、纳米晶组织结构,这些特点提高了涂层的强度和塑性、耐磨性和耐蚀性。在技术的发展过程中,也遇到了如何研发高稳定性喷涂装置、如何解释电热爆炸喷涂反应机理、如何提高喷涂效率、如何降低喷涂成本等一系列问题。若上述问题能够得到有效的解决,将极大的拓展电热爆炸喷涂工艺应用领域。
关键词:电热爆炸喷涂;表面工程;发展;技术分析;热喷涂
0 引 言
电热爆炸喷涂(Electro-thermal explosion spray)是继火焰喷涂、电弧喷涂、等离子喷涂之后发展起来的一种新的喷涂技术,又称线爆炸喷涂,它是利用金属导体(丝、片、箔)瞬间通放电发生爆炸后,产生冲击波力学效应,经过快速凝固后形成喷涂层。电热爆炸喷涂过程可扩大亚稳固熔度,生成亚稳相,减少偏析现象产生,可形成微晶和纳米晶等结构,这些特殊的组织结构使材料的物理力学性能发生显著的变化,可以提高零件表面材料的强度和塑性、增强耐磨性、提高耐蚀性、改善磁性能等[1]。
目前电热爆炸喷涂工艺已在内孔喷涂、耐摩擦磨损、抗热腐蚀等领域得到一定应用,但从国内外的研究及应用来看,基础及应用基础研究居多,实际应用情况相对较少。
1 国外电热爆炸喷涂发展状况
二十世纪五十年代末,六十年代初,金属丝电爆炸现象的研究在国外掀起了第一个高潮。六十年代初在美国波士顿接连召开三届电爆炸金属丝研究国际会议。主要是有关金属丝电爆炸机理,电爆炸金属丝雷管及应用,电爆炸断路开关等方面的研究。美国 Los.Alamos 实验室与加利福尼亚大学联合开展了电爆炸丝引爆方面的研究[2]。瑞典学者对金属丝爆炸的再触发机理进行了深入的研究[3]。
二十世纪七、八十年代,英国皇家大学材料系Hocking 报道了在大气环境下进行管件内孔喷涂的研究成果[4]。爆炸产生的金属蒸气首先到达基体并排净空气,使得随后的熔融金属颗粒在不被氧化的情况下沉积在基体表面。研究结果表明:金属液滴呈球形状,约在 2~3 μm 之间,喷射速度为 600 m/s。金属丝在轴向爆炸喷涂的情况下,约有 60 %重量的金属沉积在基体表面。涂层的厚度可达 5~15 μm,并可进行重复喷涂以使涂层变厚[5]。在 Al 和钢板上电爆炸喷涂 Mo、W、不锈钢时,所得涂层的结合强度为火焰喷涂的 5 倍。研究同时表明:当金属丝横置时,重力对金属颗粒的沉积将产生重要影响,而当金属丝竖直放置时则能达到最佳喷涂效果[6]。此外,爆炸气氛下气体压力对粒子沉积也有显著影响,较低的氛围压力使得金属蒸气快速扩散,震动波之后的能量集中程度相对较低,这样所得涂层较为均匀但厚度较薄[7]。
八十年代中期,德国学者 Grabatin 等人利用电热爆炸技术在火箭喷嘴出口段内孔喷涂铊和铌涂层的抗高温燃料气体腐蚀的实验研究[8]。试验时燃料气体的脉冲宽度为 30 ms,温度达 2 500 K,喷嘴内压力为 105kPa。在这样的环境下,上述两种涂层都呈现出极好的抗磨抗蚀特性;其中铊涂层的抗磨抗蚀性能要比铌涂层更为优越,这与燃料气体与不同金属之间的反应特性不同有关。电热爆炸过程的特性与爆炸过程中的电流和电压有关,在低电压下,释放电流呈非周期性振荡;随着电压的增高,电流趋于阻尼振荡。
日本学者在电热爆炸喷涂(线爆炸)方面起步较早,应用也较广泛。九州大学栖原教授在 20 世纪 70 年代最先开始线爆炸内孔喷涂研究,内孔线爆喷涂颗粒速度为 400~600 m/s[9]。Suhara 利用线爆喷涂方法在低碳钢基体和 Al 基体上制备 W 涂层的研究表明[10],涂层与基体结合良好,在界面区域存在一个熔焊区域。文献[11]研究了电热爆炸喷涂层的微观组织和涂层基体结合机理发现:在低碳钢上喷涂 W 涂层时,基体表面区域存在熔化现象,剪切结合强度在 200~260 MPa 范围,且认为喷涂过程中,高温、高速的喷涂颗粒是涂层基体高结合强度的原因。中村良三等人用电热爆炸的方法在SS400 钢板上喷涂了 Ni,Ni-Cr、Ni-Cr-Fe 涂层,研究了能量密度与表面粗糙度、涂层厚度、涂层硬度以及结合强度的关系[12]。近腾龙彦等研究了电热爆炸喷涂法制备 Al+W 复合涂层体系[13]。今井田等研究了基体表面温度对电热爆炸喷涂层性能的影响[14,15]。
2 国内电热爆炸喷涂发展状况
国内对金属丝电爆炸现象的研究方面,一些科研院所及大学主要是利用金属箔(丝)经快速加热爆炸之后产生的冲击波力学效应、并结合快速凝固技术进行工业应用,例如爆炸喷涂、除垢、模拟水中核爆炸、模拟震源、污水处理、液电成型等[16,17]。其中总参工程兵科研三所的张六一等人在二十世纪七十年代对金属丝爆炸冲击波进行了实验和理论研究[18]。中科院流体物理所与西安 24 所联合开展电爆炸金属材料的研究[19]。吉林大学超硬材料国家重点实验室利用电爆炸制备金属纳米微粉[20]。国防科技大学研究激励气体产生的近红外强光辐射的物理过程及机理[21]。华中理工大学研究了水中金属丝电热爆炸的压力特性[22]。
华北电力大学刘宗德教授近年来在电热爆炸金属材料、电热爆炸等离子体随时间的演化关系等方面进行了相应研究,已成功地将电热爆炸金属丝开关应用到脉冲功率技术中[23~26],研制了电热爆炸定向喷涂装置,并初步制备了具有超细晶、纳米晶组织结构的涂层,涂层具有晶粒细化、低孔隙率、高结合强度等诸多优点,能形成具有良好的抗磨损性能的金属陶瓷涂层,所制备的电热爆炸喷涂层已在电厂测温热电偶护套外表面成功应用。
装备再制造技术国防科技重点实验室与华北电力大学合作,利用定向电热爆炸喷涂装置,制备了具有纳米结构的防腐、耐磨涂层体系[27~30]。其中FeCrAlRE 电热爆炸喷涂层成功应用于重载车辆废旧发动机排烟管抗热腐蚀研究领域,NiCr–Cr3C2涂层应用于重载车辆废旧扭力轴盖耐摩擦磨损的试验研究。通过与新品件一同进行实车考核,施加了电热爆炸喷涂层的两种再制造件分别在防腐、耐磨领域表现出优异的性能,其防腐、耐磨寿命分别较新品件延长了 2~4 倍,从而提高了零件的重复利用率,实现了节能、节排、环保的目的。
3 电热爆炸喷涂的关键技术问题
3.1 电热爆炸喷涂的反应过程
电热爆炸反应的特殊性,决定了在很多领域有潜在的应用价值,如材料表面喷涂、超细粉末制备、脉冲高压电源、等离子体聚爆、模拟核爆炸等。此外,电热爆炸技术在材料加工领域的应用同样受到广泛的关注,尤其是在超细粉末制备和表面喷涂领域,近年来已经取得了一定的进展。华北电力大学、装备再制造技术国防科技重点实验室等单位共同承担的国家“863”研究课题初步认为电热爆炸喷涂反应过程分为 4 个阶段:
① 金属导体固态加热阶段。储能电容向金属导体(丝、片、箔)瞬时放电,施加强大电流使导体加热逐步趋向熔化;
② 金属导体熔化、气化阶段。欧姆加热的持续作用促使导体熔化、气化,熔融的导体破裂成液滴,并产生等离子体,由于电磁箍缩效应及周围介质气体的冷却作用使蒸汽的膨胀受到限制而产生内部高压,最终导致金属导体发生爆炸反应;
③ 电热爆炸阶段。高温金属蒸气及粒子以约2000 m/s 的速度膨胀,同时产生冲击波,驱使金属蒸气与介质气体分子剧烈碰撞,并以很高的速度冷却下来,形成簇团或超细颗粒,喷射到材料表面沉积后形成性能优良的涂层。当金属颗粒高速运动过程中,如果与气体发生化学反应,将形成金属化合物。如果电容储存足够多的电能,将在爆炸后的粉末颗粒和介质气氛中继续放电。在此过程中,电流密度达 107~109A/cm2,放电功率高达 100~200MW,放电时间约为 100~500 μs;④ 冷凝阶段。几乎达到沸点的散射金属粒子在与基体材料碰撞过程中 10-8s 即可固化,金属粒子以 107~109km/s 的速度冷却。电热爆炸喷涂装置电路图如图 1 所示,图 2 为电热爆炸喷涂装置示意图。目前电热爆炸喷涂工艺可以制备 Fe 基、Ni 基、Ti 基等不同组分的涂层体系。尽管电热爆炸喷涂技术表现出了优异的性能,但其尚属起步阶段,反应过程中还存在很多尚未解
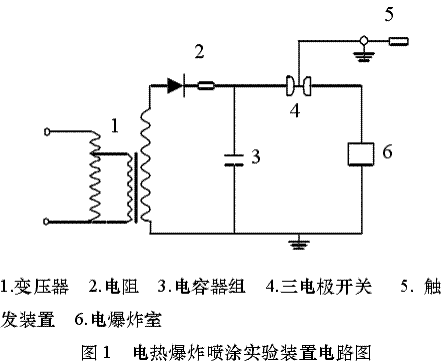 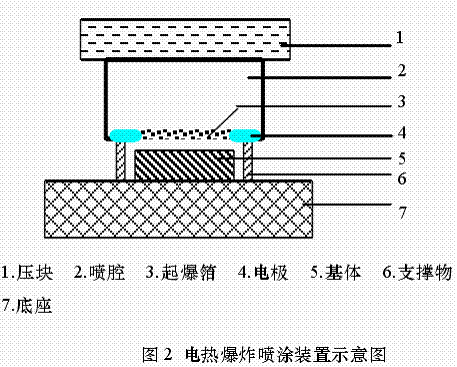
释清楚的反应机理问题,例如电热爆炸喷涂反应阶段如何定量划分,更有针对性的了解反应过程,进而能有效的控制反应过程,例如通过人为的延长金属导体熔化、气化阶段,或人为的缩短冷凝阶段,来观察和探索电爆炸喷涂反应过程的实质。因此,电热爆炸喷涂反应过程的研究还应从整个体系的反应动力学、热力学以及喷涂粒子的沉积路径等几方面进行深入分析。
3.2 电热爆炸喷涂层的组织结构和结合强度
结合试验结果及应用分析,认为电热爆炸喷涂层与基体的组织结构、结合强度关系主要受反应时间、反应过程能量加载以及反应过程中气化金属粒子的行为等几方面因素的影响。因此,需要分析影响涂层组织结构和结合强度的因素,才能改善涂层的组织结构,增强涂层与基体的结合强度。
① 电热爆炸反应时间的影响。 电热爆炸喷涂层与基体的结合强度在很大程度上依赖于喷涂粒子喷射时的动能。粒子飞行速度越快,其动能越大,对基体表面的撞击程度也越大,这将促进涂层与基体的结合。由于电热爆炸喷涂反应在瞬间发生,反应过程中积聚了相当大的能量,并在瞬间释放能量,同时发生冷却过程,从而提高喷涂层与基体的结合强度。
② 能量加载的影响。 喷涂粒子内部热焓值大小是决定涂层与基体形成冶金结合的重要因素。热焓值越高,粒子内部温度越高,加速了粒子熔融的进程。当熔化态或气态的粒子以极高的速度喷射到基体表面,粒子发生剧烈变形并瞬间凝固时,粒子之间进行了充分的物理接触。当喷涂熔滴或蒸气到达基体表面的温度高于基体熔点时,喷涂粒子与基体之间结合将由机械结合向冶金结合过渡。由于电热爆炸喷涂装置的喷腔形状呈敞开式,粒子在喷射过程中,压力逐渐降低,喷射时间缩短,导致喷涂粒子的热焓损失减少,这样喷涂粒子到达基体表面时仍具有相当高的热焓值,粒子与活化基体表面相互作用,将有利于涂层与基体结合强度的提高。
③ 气化金属的影响。 涂层与基体、涂层与涂层之间的致密度是影响涂层与基体结合强度的重要因素之一,由于涂层越致密,其孔隙率越低,涂层与基体结合强度也就越高。而涂层的致密度由熔化或气化的金属粒子大小来决定,金属粒子大则涂层表面粗糙,金属粒子小则涂层表面致密。此外,涂层的孔隙率还与喷涂过程中粒子的温度和速度有关,由于电热爆炸反应产生的粒子温度极高,粒子喷射速度可达 3000~4500 km/s,因此粒子在与基体接触的快速冷凝过程中,在极短的时间内粒子由气态或熔融态转变成固态,使得金属粒子的尺寸明显降低,涂层组织得以细化可达到微纳米结构,从而可以形成致密涂层。
综合三种影响因素的分析,对于改善电热爆炸喷涂层组织结构、提高结合强度的有效途径,可归纳如下:① 尽量缩短爆炸反应时间;② 拉近喷腔与基材的距离,缩短粒子的行走路径,最大限度的保持粒子内部的热焓,促进涂层与基体形成冶金结合。
3.3 高电压、高稳定、高效率电热爆炸喷涂装置研发
从电热爆炸喷涂反应动力学分析来看,随着喷涂电压的增高,反应体系的内聚及释放的能量将剧增,产生的冲击波力学强度也将呈几何数量级的倍数增加,所制备出的涂层组织结构将更加致密,同时涂层与基体的结合强度也将更加增强。但其负面的影响也将会出现,即可能会出现后一层喷涂时将前一层涂层打飞、减薄的现象。改善这一问题的措施可以采取前几层喷涂时,喷腔与基体距离近些(10 mm 左右),后几层升高喷腔与基体之间距离(20 mm 左右)的方法,确保在高电压喷涂状况下,一方面保证涂层与基体的结合强度,另一方面又可以保障喷涂层的厚度。
由于电热爆炸喷涂装置的核心大多为电子元器件,诸如高压变压器、高压整流硅堆、充电电阻、储能电容器组等,由于喷涂反应过程是瞬间充电、瞬间放电的过程,对电子元器件的承载能力考验极大,其寿命的长短决定了电热爆炸喷涂装置的稳定性。因此,需要选取耐用的、高承载能力的电子元器件,从而确保喷涂装置的作业稳定性。针对目前电热爆炸喷涂反应效率低的不足,可从 3 个方面加以改进:① 力争实现喷涂材料(起爆丝)的自动更换,减少因更换喷涂材料而浪费的时间;② 增加喷腔数量,实现一次装填喷涂材料,多个喷腔逐个或同时起爆;③ 点阵式分布喷涂材料(起爆丝),逐点或多点同时发生喷涂反应。
3.4 电热爆炸喷涂反应能量的利用率
利用高压大电流脉冲放电技术的电热爆炸喷涂工艺,反应体系中能量的利用程度在研究过程中受到广泛关注。反应过程中喷涂材料经历了加热、熔化、汽化、爆炸、冷凝等各阶段,通过对反应过程的动力特性分析,可以得到喷涂瞬态过程中电压、电流功率和电阻等参数的变化特性,利用示波器采集到瞬时喷涂电流与喷涂电压的波形曲线,通过积分计算反应过程中消耗能量,即2221E =CU,电容器储能由式∫E= Pdt1计算出不同电压下电容器的储能。而电容器输出能量与电容器储能之比即为电热爆炸反应的能量利用率(η)。以 FeCrAlRE 电热爆炸喷涂反应能量利用率计算为例,按照计算公式,分别得出了不同喷涂电压(3 000 V、4 000 V、5 000 V)条件下,电热爆炸反应体系的能量利用率分别为 36.1 %、49.5 %、67.7 %。结果表明随着喷涂电压的增高,反应体系的能量利用率也相应增加。
由于喷涂材料的加热速率、电流密度决定着能量密度,而能量密度对喷涂材料的爆炸反应、喷射速度影响很大,因此在电流密度变化不大的情况下分析能量的利用比率对于确定不同物性的喷涂材料爆炸参数具有实际意义。尤其是在当前“节能减排”的大形势下,如何避免高耗能、如何提高反应的能量利用率,将是电热爆炸喷涂工艺发展的一大瓶颈问题。
3.5 降低电热爆炸喷涂的材料成本
目前电热爆炸喷涂采用的喷涂材料为金属丝/片/箔,一般是首先通过设计喷涂材料成分后铸锭,再利用线切割制成所需尺寸的喷涂材料,其加工成本高,且周期长,同时不宜安装(过薄易折)。因此,可以将喷涂材料改成金属粉末,直接喷涂金属粉,降低因铸锭、线切割制片所产生的间接费用,同时缩短安装喷涂材料的周期。
4 结 论
(1) 电热爆炸喷涂技术是一项新兴的且具有一定发展前景的喷涂技术,其制备的喷涂层组织致密,孔隙率低,可以形成微米晶、纳米晶组织结构,尤其是在解决小直径孔类零件内、外表面喷涂方面具有独特的优势。
(2) 电热爆炸喷涂工艺还存在一些需要改进的环节,诸如保障喷涂装置稳定性、降低喷涂成本、提高喷涂效率、提高喷涂过程的能量利用率等,这些环节若得到改进,将大大提高电热爆炸喷涂工艺的应用领域。
致 谢:
论文内容在研究过程中得到了华北电力大学刘宗德教授的大力协助,在此深表感谢!
参考文献:
[1] 徐滨士, 等. 再制造工程基础及其应用 [M]. 哈尔滨: 哈尔滨工业大学出版社, 2005.
[2] 李业勋. 金属丝电爆炸机理及特性研究 [D]. 绵阳:中国核物理研究院, 2001.
[3] Vlastōs A E. Near-infrared radiation intensily from restrikes of exploding wires [J]. Journal of Applied Physics. 1968,38(7):3081-3083.
[4] Hocking M G. Thermal plasma weld and detonation[M]. 1975: 168-175.
[5] Grabatin H, Schlett V, Stuke H, et al. Resistance of tantalum and columbium coating to propellant gas erosion [J]. Journal of Vacuum Science Technology.1985, 3(6): 2545-2550.
[6] Mizusako F, Tamura H, Horioka K, et al. Zr-O-Bceramics/Ni-20%Cr alloy graded coating produced by electrothermal explosion spraying [J]. Surface and Coating Technology. 2004, 187(2-3): 257-264.
[7] Kodama T, Keda Y, Tamura H. Reactive thermal spray by high velocity ceramic jet and characterization of the coatings [J]. Journal of Thermal Spray Technology. 1999, 8(4): 537-544.
[8] Kawahara Y. Evaluation of new corrosion-resistant superheater tubing in high-efficiency waste-to-energy plants [J]. Corrosion. 1998, 54(7): 576-589.
[9] Tamura H, Konoue M, Sawaoka A B. Zirconium boride and tantalum carbide coatings sprayed by electrothermal explosion of powders [J]. Journal of Thermal Spray Technology. 1997, 6(4): 463-468.
[10] Suhara T, Eng D, Kltajima K. Coatings by wire explosion spraying-properties and applications [C].6th International Metal Spraying Conference, Paris,1970, B: 179-184.
[11] Suhara T, Kitajima K, Fukuda S. The structure and adhension of coatings deposited by wire explosion spraying [J]. Journal of Vacuum Science Technology.1974, 11(4): 787-792.
[12] Nakamura R, Fukuzumi K. Coating properties of Ni and Ni alloys seposited by wire explosion spraying method [J]. Welding Journal. 2000, 38(3):127-133.
[13] Kondo T, Hasebe T, Imaida Y. Wire explosion spraying for composite coating [C]. The 51thJapanese Joint for the Technology of Plasticity.2000: 27-28.
[14] Tamura H. Effect of surface temperature of substrate in explosion spraying [C]. The 50th Japanese Joint Conference for the technology of plasticity. 1999:249-250.
[15] Tamura H, Ogura T, Nagahama M. Spraying of the brittle ceramic zirconium diboride by a wire explosion technique [J]. Journal of Applied of Physics. 1994,75(3): 1789-1797.
[16] 卢新培, 张寒虹, 潘垣, 等. 水中脉冲放电的压力特性研究 [J]. 爆炸与冲击, 2001, 21(4): 282-286.
[17] 朱亮, 张周伍. 电爆技术用于超细粉末和表面喷涂的研究进展 [J]. 材料导报, 2005, 19(12): 76-79.
[18] 张六一. 金属丝爆炸流体动力学方程的数值解法[C]. 第四届全国计算流体力学会议论文集, 1988, 10.
[19] 盛季胜, 王依野. 金属丝线爆熔射涂层法 [J]. 表面技术, 1992, 21(2): 83-85.
[20] 王群. 电爆炸方法制备纳米微粉及其物性研究 [D].吉林: 吉林大学, 1999.
[21] 张晓萍. 电爆炸丝爆炸冲击波激励气体红外脉冲强光辐射产生机理的研究 [D]. 长沙: 国防科技大学,2000.
[22] 吴为民, 刘娆, 张玉萱. 线爆喷涂技术的研究 [J].电工电能新技术. 1994, 1: 32-36.
[23] 刘宗德, 杨昆, 段鹏, 等. 线爆炸法制备 WC-Co硬质合金涂层的实验研究 [J]. 爆炸与冲击.2003, 23(2): 116-121.
[24] 刘宗德, 杨昆, 安江英, 等. 纳米材料及其在电力工业中应用前景 [J]. 现代电力, 2001, 18(4):1-5.
[25] 蒲泽林. 电热爆炸法制备亚微米晶涂层的研究 [D].北京: 华北电力大学, 2005.
[26] 徐亮. 电热爆炸超高速喷涂法制备 NiAl-TiC 复合涂层的实验研究 [D]. 北京: 华北电力大学, 2005.
[27] Wei Shi-cheng, Xu Bin-shi, Wang Hai-dou, et al.Comparison on corrosion-resistance performance of electro-thermal explosion plasma spraying FeAl-base coatings [J]. Surface & Coatings Technology. 2007(201): 5294-5297.
[28] Wei Shi-cheng, Xu Bin-shi, Wang Hai-dou, et al.High-Temperature corrosion-resistance performance of electron-thermal explosion plasma spraying coating FeAl-base coatings [J]. Surface & Coatings Technology. 2007(201):6768-6771.
[29] 金国, 徐滨士, 王海斗, 等. 电热爆炸喷涂 WC/Co涂层组织性能研究 [J]. 金属热处理. 2006, 342(31):23-25.
[30] Jin G., Xu B S, Wang H D, et al. Microstructure and wear resistance performance of the electro-thermal explosion sprayed stellite coating used for remanufacturing [J]. Journal of central south university of technology. 2005, 12(suppl. 2): 207-210
本站文章未经允许不得转载;如欲转载请注明出处,北京桑尧科技开发有限公司网址:http://www.sunspraying.com/
|