阳极金属热喷涂涂层耐久性研究进展
田云生,晁 兵,白书亚,张同标,谢 谦
施 工 技 术2010 年 12 月
[摘要]介绍了阳极金属热喷涂涂层耐久性试验方法、检测评价方法以及研究进展情况,对现有成果进行了分析总结,探讨了存在的一些问题,期待取得新的进展。
[关键词]阳极金属;热喷涂;涂层;阴极保护;电化学
从 20 世纪 20 年代至今,采用 Zn、Al 阳极金属及其合金(如 Zn/Al、Al/Mg、Al/Mg/Zn、Al/Mg/Re 等)热喷涂涂层对钢铁构件、建筑物进行长效腐蚀防护的技术得到了本行业内的普遍认可和持续发展,虽然其应用及防护效果获得了一致肯定,但对其长效防护性能的测试评价技术仍在不断的改进、完善与创新中。由于各类阳性金属热喷涂涂层防护性能的评价结果不仅影响到其自身的应用与推广,还牵扯到各相关方的经济利益,其测试技术及结果的真实性、可靠性和精确性更值得大家的积极探讨与创新提高。
1 试验方法
阳极金属热喷涂涂层应进行封闭处理,根据防护需要还要进行中涂和面涂处理,一般不单独使用,其单层性能的评价指标主要有外观、厚度、空隙率、孔隙率、硬度、附着力(结合强度)及耐久性,耐久性性能一般结合防护体系设计方案,与封闭层或底漆、中间漆、面漆 3 层形成复合涂层后进行评价。参照涂料涂层的试验方法,单层阳极金属涂层耐久性的测试评价根据使用环境不同有耐气、雾试验(如耐中性盐雾试验、耐SO2气氛试验)、耐介质浸渍试验(如耐酸雨试验、耐碱液试验、海水全浸试验)以及环境循环试验(如盐雾-老化循环试验、各类介质间交替试验)等。
2 检测评价方法
阳极金属热喷涂涂层对底材具有屏蔽和阴极保护的双重防护作用,其耐久性检测方法主要有目测、电化学方法、失重法、图谱法及上述检测的综合分析方法。
2. 1 目测
主要观察涂层试验中表面状态的变化情况,通过对腐蚀现象(如氧化、渗锈、脱落等)最早出现的时间进行对比,评价各类涂层的防护效果,可用于各种试验方法中。
2. 2 电化学方法
目前电化学检测是应用最普遍也是最可靠的方法,有许多优点:测试方便快捷、破坏少、获得与涂层防护性能相关的直接信息量大,同时能对金属的腐蚀机理及涂层失效行为进行更深入的研究。涂料涂层电化学测试方法有直流法、电化学阻抗谱法、电化学噪声法、扫描开尔文探针及扫描振动电极等,目前应用于阳极金属涂层检测的主要是直流电化学法、电化学阻抗谱法,其中直流电化学法有电位-时间法、极化曲线法和极化电阻法等。该方法主要用于金属涂层裸露试样的试验中。
2. 3 失重法
检测试样测试前后质量的变化,对失重/增重的变化过程、趋势及大小等进行分析对比,判定各类涂层的防护效果,一般用于金属涂层裸露的试验。
2. 4 图谱法
采用扫描电镜(SEM)、X 射线衍射仪、金相分析等现代化仪器测试分析阳极金属涂层微观结构、成分等的变化,剖析其腐蚀机理及防护效果。
2. 5 综合分析方法
由于阳极金属热喷涂涂层防护机理的多样性以及环境影响的复杂性,仅凭单一项目的测试很难对其防护效果做出准确可靠的评价,需要将上述各种方法(如3 种) 的检测结果结合起来,进行综合分析后做出最终评价。
3 研究结果
3. 1 腐蚀机理
3. 1. 1 单一阳极金属热喷涂涂层
侵入的腐蚀介质首先被阳极金属消耗,产生的金属氧化物能够在一定程度上加强热喷涂金属涂层的屏蔽性能;当腐蚀介质抵达基体表面时,电偶腐蚀形成,阳极金属开始对基体发挥阴极保护作用,只有当阳极金属涂层损失到一定的程度后(极限有效保护厚度),才逐渐丧失对钢铁基体的阴极保护作用,其腐蚀防护寿命即行终止。
上述机理得到普遍认可,但对于 Al 涂层而言,腐蚀机理可能要更复杂一些,由于 Al 的阴极保护作用明显弱于 Zn,在腐蚀介质渗透 Al 涂层到达基体表面的过程中,腐蚀物质只能被 Al 消耗一部,仍有一部分腐蚀物质能够到达金属涂层与基体的接触界面,Al 涂层表面快速出现的褐斑即是底材腐蚀产生亚铁氧化物渗出形成的,伴随着腐蚀介质的持续作用,在 Al 涂层表面、内部以及金属涂层与基体的接触界面,Al 的氧化、溶解以及基体的腐蚀几乎在同时或快或慢地进行着;孙建波等人研究表明在缺氧环境下,Al 难于钝化而易于溶解,能发挥出较好的阴极保护作用。
3. 1. 2 两种以上阳极金属热喷涂涂层
1)合金涂层
目前的合金涂层主要采用 Zn-15%Al 合金、Al-5%Mg 铝镁合金、Al / Mg / Re 合金线材喷涂制得。Zn-15%Al 合金涂层的应用较广,涂层由富锌相 ( Al55% /Zn45%)与富铝相(Zn95% /Al5%)组成,富铝相在组成涂层的颗粒范围内成连续框架网络,富铝相化学稳定性好,为富锌相提供保护,电化学防护性能不如锌,但优于纯铝,涂层孔隙率少、快速自封闭特性好,腐蚀发生时合金涂层中锌元素优先溶解;Zn-15%Al 合金的电化学性能在静态特性与锌相似而动态环境与铝相似,不同铝含量的锌铝合金涂层试样的阳极极化曲线都类似与纯锌涂层试样;而采用开路电位-时间法研究加入不同铝含量的富锌涂层在 3. 5% NaCl 中的腐蚀行为,随着铝含量的升高开路电位正移,从而增强涂层的防护性能,表明铝的加入能阻止锌的腐蚀,但当铝含量增加到 75%时开路电位迅速正移甚至超过铁的开路电位,牺牲阳极作用消失。
Al-5% Mg 铝镁合金涂层在 0. 86mol / dm3盐水中的腐蚀电位约为-1. 2V,性能比纯铝层活泼,对基体的阴极保护作用增强,在腐蚀介质侵入过程中,有较好的阻塞孔隙自封闭能力,破损时也能发挥更有效保护作用。Al/Mg/Re 合金中随稀土加入量不同,稀土元素可以偏聚在相界、晶界和枝晶界或固溶在化合物中或以化合物形式存在,主要通过细化涂层合金组织,降低其孔隙度、提高涂层与基体的结合力来提升涂层耐蚀性。
2)热喷涂伪合金涂层
伪合金涂层是采用两种不同金属丝材电弧喷涂制得的,其防护性一般能同时具有两种金属涂层的耐蚀优点,各自的缺点则得到一定程度的弥补,目前应用的主要组合模式有锌丝 + 铝丝、锌丝 + 铝镁合金丝。锌丝 + 铝丝喷涂形成的锌铝伪合金涂层由纯锌相、纯铝相及少量的锌-铝合金相组成,锌铝体积比约 1∶ 1,质量比约 73∶ 27,3% 盐水中腐蚀电位-1. 30V,腐蚀电流 100μA/cm2,电化学性能介于锌、铝之间但更接近于锌,涂层机械性能则接近于铝,其腐蚀机理是将 Zn的阴极保护作用与 Al 的屏蔽耐蚀性能结合起来抵御腐蚀介质浸蚀。锌丝 + 铝镁合金丝主要组成是锌、镁铝合金的机械混合物以及一些富锌、富铝合金相,涂层中有一些富铝的氧化物薄膜,膜中含镁约 1. 9%,其防护机理与锌铝伪合金涂层近似。
3. 1. 3 涂层中氧化物的作用
对涂层中氧化物的作用目前褒贬不一,锌的腐蚀产物由于溶解度偏高,业内公认其在腐蚀过程中只具有一定的屏蔽和自封闭作用,过多的氧化锌不利于提高 Zn 涂层的耐蚀性,如湿度达到 70% 时锌的腐蚀产物通过吸收充足水分促进腐蚀发展;而氧化铝致密、抗蚀、氧化膜导电率低、自愈能力强,其屏蔽作用显著提高了铝涂层的耐蚀性,但氧化膜的存在也影响了 Al 阴极保护作用的发挥;含镁金属涂层中有一些富铝的氧化物薄膜,镁氧化优先形成尖晶石结构的氧化物,在腐蚀介质中,比氧化铝有较好的阻塞孔隙自封闭能力;稀土金属涂层中,稀土元素强化细晶,改变了铝合金表面的氧化膜结构,增加了氧化膜厚度,其屏蔽、耐蚀性能得到明显提高。
现有研究表明,小半径阴离子(如 F-、Cl-等)易渗透并破坏氧化膜的屏蔽作用,而丝材在喷涂过程中阳极金属形成的氧化膜其耐蚀性也明显低于经化学处理形成的氧化膜(如 Al)。笔者选用 4 种丝材(Zn、Al、Zn / Al、Al / Mg),测量其打磨前后在 3. 5% 盐水、模拟酸雨(pH =5)的腐蚀电流变化,结果表明,在 3. 5% 盐水中原有氧化膜基本未发挥屏蔽作用,而在模拟酸雨(pH = 5)中各类丝材表面的原有氧化膜都发挥出了一定的屏蔽作用。
3. 1. 4 热喷涂金属涂层中的金属片
在大气环境中所喷涂的典型阳极金属涂层主要是由阳极金属颗粒、氧化物杂质及孔隙所组成的一种非均质混合物,涂层与基体之间依靠机械结合或部分的冶金结合黏结在一起,而涂层的自身则靠相互齿合的内聚力而形成一体。刘燕等人的研究表明金属涂层腐蚀后,表面由一层一层的片状腐蚀产物结合而成;孙建波等人的研究表明,金属颗粒形变后其很多部位处于活化态,与钝态氧化膜形成活性-钝性腐蚀微电池,纯态铝作为牺牲阳极被腐蚀,在腐蚀介质及腐蚀产物的“解理作用”下,片状颗粒之间的机械嵌合力减弱或消失,形成片状剥离脱落,局部最终成为腐蚀坑。
3. 2 防护效果
3. 2. 1 防护寿命
1)国外研究成果
英国国家标准学会(BSI)在 1977 年制定的钢铁结构件防腐蚀技术标准(BS 5493-1977)中指出:只有热喷涂的锌或铝涂层才能保证钢铁结构件在工业及海洋大气中 20 年不需维护。加拿大标准协会确认,热喷涂锌或铝涂层方法可以给予钢铁构件预期 40 年的保护寿命。
美国焊接学会热喷涂委员会 19 年的现场挂片试验表明,厚度 0.08 ~0.15mm 的铝涂层,不论是否封孔都能保证钢铁基体在海水、严酷的工业大气及海洋大气中 19 年不腐蚀;要保证钢铁基体在严酷的工业大气和海洋大气中 19 年不腐蚀,不经封孔处理的喷锌涂层厚度 至 少 为 0. 23mm,在 海 水 中 锌 涂 层 厚 度 至 少0. 3mm;经过封孔处理锌涂层的厚度减至 0. 08 ~0. 15mm,也可达到上述防腐效果。从应用试验的研究结果来看,80μm 热喷铝涂层海滨暴露 34 年后其钢铁基体未发生腐蚀现象,前苏联试验表明 120μm 铝涂层在盐雾腐蚀环境下寿命达20 ~25 年,Garland P O 等人研究得出 200μm 铝涂层防腐寿命超过 60 年,20 世纪中后期以来,国际上逐渐选择喷 Al 涂层取代 Zn 涂层作为大型工程防护的首选。
2) 国内研究成果
现有研究成果表明,普通电弧喷铝涂层在中性盐雾(pH 值 7. 0 左右) 环境中的深度腐蚀速率为4. 33μm/年,在煤矿井水(pH 值 6. 5-8. 9)深度腐蚀速率为2. 5 ~ 6. 5μm / 年,安云岐等人研究表明,在酸雨条件下,深度腐蚀速率为 1. 9-2. 2μm/年大功率二次雾化电弧喷铝涂层防护寿命。茅兆祥研究认为 120μm 锌铝伪合金涂层能够满足 50 年防腐寿命要求。
3. 2. 2 防护差异
萧以德等人在 3 个海域全浸、潮差和飞溅区 3 个腐蚀区带进行 8 年的海水暴露试验表明,喷锌铝/封闭和喷铝/封闭体系是在海水中对钢铁起长久有效保护的可靠方法,其中喷锌铝/封闭体系的保护性能更佳,推荐采用喷锌铝、喷锌和无机富锌涂料作底涂层;赖国伟等人实海试验表明,在飞溅区、在潮差区和全浸区,锌铝合金涂层的腐蚀面积小于铝涂层及锌涂层;夏兰廷等在青岛、厦门、榆林 3 个试验站的飞溅区、潮差区、全浸区进行了 4 年海水腐蚀性能研究,证明铝、锌涂层在静海全浸条件下具有优良的耐腐蚀性,铝涂层好于锌涂层;董立先等人对纯铝涂层、锌铝伪合金涂层的动态腐蚀试验表明,纯铝涂层耐蚀性能优于锌铝伪合金涂层;李秉忠等人 2 000h 盐雾试验结果表明,锌铝伪合金涂层的结合强度和耐蚀性能均优于 Zn-15% Al 合金涂层,接近纯铝涂层;陈长江、李秉忠 2009 年对锌铝伪合金涂层电化学机理研究表明,抗腐蚀性能优劣顺序为纯铝层、锌铝伪合金、纯锌层。陈永雄、徐滨士等人研究表明,向 Zn-Al 合金中加入其它适量元素能显著改善涂层耐蚀性能。
多方研究表明,在盐雾、海洋环境及酸雨下,Al、Zn、Al / Zn(合金)、Al-Zn(伪合金)4 种电弧喷涂涂层中,耐蚀性综合评价明显存在争议,多数研究结果表明Al 最佳,其它依次是 Al-Zn、Al / Zn、Zn。
3. 2. 3 防护方案
目前国内采用的防护方案中,阳极金属热喷涂涂层主要有 Al、Zn-15% Al、Zn + Al 三类,目前喷铝方案在国内外应用最为广泛,喷铝方案如表 1 所示,Zn-15% Al 与 Zn + Al 基本方案为(140 ± 20)μm.
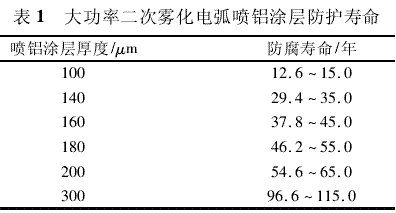
3. 2. 4 应用效果
目前喷铝工程在国际上已有众多成功应用 50 年以上的大型工程案例,国内大型喷铝工程最早的为武汉军山长江公路大桥,其复合涂层使用 10 年来对钢箱梁防护良好。重庆鱼嘴长江大桥为锌铝伪合金涂层的代表工程,在建的青岛海湾大桥为锌铝合金涂层的代表工程。
3. 3 其他进展
中科院金属所郑立群等人利用交流阻抗和弱极化相结合技术,在 CMB-1510B 等的基础上研制了 CMB-4510 测量仪,有效解决了线性极化技术及介质电阻存在的误差。
装甲兵工程学院从 1997 年即开始研究稀土元素加入技术对提高金属涂层耐蚀性能影响,发表的成果表明稀土金属元素促进铝涂层颗粒细化降低孔隙率、增加铝涂层强度和塑性、显著降低了硫、硅及氢等元素的不良影响,涂层耐蚀性能明显提高。
4 存在问题
从上述研究结果可以看到,对热喷涂阳极金属涂层耐蚀性能的评价结果存在极大争议性,主要原因就是现有试验及检测评价技术还存在较多问题,需要更进一步的改进。
4. 1 测量方法的影响
4. 1. 1 电化学方法的局限
电化学阻抗谱法有其局限性,为了得到塔菲尔直线段需要将电极极化到强极化区,电极电势偏离自腐蚀电势较远,这时的阴极或阳极过程可能与自腐蚀电势下的有明显的不同;其次,由于极化到 Tafel 直线段,所需电流较大,容易引起电极表面状态、真实表面积和周围介质的显著变化。因此要求每一次试验使用一个新的样品,不利于比较性研究。弱极化法测量虽然避免了强极化法对腐蚀体系扰动过大、线性极化法由于近似处理存在的明显误差,但忽视了介质电阻等对测量的影响,影响腐蚀电位的主要有涂层电阻、因金属离子和 OH-等腐蚀产物扩散缓慢造成的浓度梯度和缓蚀剂对腐蚀的抑制作用等。
由于影响电位的因素很多,不同涂层腐蚀电位含义不同,在实际操作中应针对不同类型涂层的金属做不同分析,对测定结果的解释应慎重,通常情况下需要结合其他方法综合分析。
4. 1. 2 失重法的计量
热喷涂阳极金属涂层试样腐蚀产物(氧化物)的去除一直未有简捷、准确、可靠的方法,因为涂层在喷制形成过程中,形成大量的氧化物,涂层中还夹杂了许多颗粒,试验中,表面的氧化物及杂质很容易脱落,清洗时也无法保证原有氧化物不被清洗掉,这对试验结果产生了较大影响。另外失重法评价的更应是金属涂层自身的耐蚀性,并不能用来直接衡量其对金属涂层的保护性能。
4. 2 试样质量的影响
喷涂涂层的孔隙率、密实度以及底材的表面处理质量和涂层结合强度等都是影响金属涂层腐蚀性能测量可靠性的重要因素;金属涂层表面也不能等同于平面处理,即使严格控制喷涂工艺,涂层也存在大量空隙、表面高低误差达到几十微米,而腐蚀介质也能轻易渗透到涂层内部,因此其表面积很难准确计量,一些研究者以及测试方法简单采用平面对待,结果会产生较大偏差。
4. 3 腐蚀介质的影响
实验室条件下进行的研究试验,腐蚀介质一般都是封闭或半封闭体系,与环境的开放体系不同;测试过程中即使腐蚀介质整体处于动态循环过程中,其腐蚀物质的消耗也是具有明显变化趋势的,那些腐蚀介质用量少、介质更换或补充频率低、数据测取时机偏颇的研究结果就会出现较大问题。现有研究也表明,试验介质的温度、溶解氧含量甚至试样在介质中的位置都对腐蚀结果产生一定影响。
4. 4 试验条件的局限性
虽然学术界不少人接受钢结构中性盐雾加速试验200h 代表钢结构使用 1 年的观点,但试验条件始终无法准确模拟实际的环境条件,试样的制备工艺也与大规模涂装施工的工艺条件存在明显偏差。研究表明室内模拟试验与大气暴露试验之间的加速性不是一个简单常数,而是随时间呈动态变化,自然倍受各种因素影响的阳极金属涂层研究结果也就出现了很多争议。
5 结语
阳极金属热喷涂涂层技术为我国的煤矿、电力、桥梁等工程防护以及机械设备的维修翻新等做出了重大贡献,其防护性能也得到了国内外众多试验及工程实例应用的验证,但其试验、检测及评价过程中存在的诸多技术问题引起了业界不少专家学者的激烈辩争,如何能够实现准确、可靠、定量地评定其防腐性能,需要大家的深入探讨与共同努力。
参考文献略
本站文章未经允许不得转载;如欲转载请注明出处,北京桑尧科技开发有限公司网址:http://www.sunspraying.com/
|