微缺陷对热喷涂涂层接触疲劳性能的影响
土韶百,李国禄,土海斗,刘金海,徐滨士,朴钟宇
(1河北工业大学材料科学与工程学院.天津300130;
2装甲兵工程学院装备再制造技术国防科技重点实验室.北京100072)
摘要:采用超音速等离子喷涂设备在朽号钢基体上制备了甲种含有不同微缺陷的ViCrF'}Si合金涂层。使用球盘式接触疲劳实验机对涂层的接触疲劳性能进行了测试.建立了Wcibull失效概率图:使用扫描电子显微镜对涂层的微观结构和失效形貌进行了表征:比较了甲种涂层的接触疲劳寿命及涂层的主要疲劳失效模式。结果表明.涂层内的微缺陷主要由微孔隙和微裂纹构成.涂层接触疲劳寿命的长短与这此微缺陷含量的多少成反比.同时.涂层微缺陷含量较少时涂层的失效模式主要以剥落失效为主:涂层微缺陷含量较多、结合强度较差时主要以分层失效为主:涂层内存在较大的孔隙可致使涂层的提早失效.同时涂层表面磨损失效的概率增加。
关键词:等离子喷涂:微缺陷:失效模式:接触疲劳寿命:Wcibull分布
接触疲劳是指工件在交变接触压应力长期作用下.接触表面局部区域产生小片或小块状剥落而使工件失效的现象。轴承、齿轮、轮轨等都是在长期交变的滑动或滚动接触应力作用下发生接触疲劳而失效的.由于疲劳失效没有明显的征兆.因此极大地威胁了生产安全。研究表明.热喷涂技术可以改善工件表面的综合性能.可以有效提高工件的接触疲劳寿命。热喷涂涂层是由高温熔滴撞击基体或已形成的涂层表面.之后经过扁平变形、冷却凝固而成的.这一过程致使涂层内部不可避免地存在有微孔隙、微裂纹等缺陷比。这些微裂纹的数量和形态对涂层的接触疲劳寿命有何影响.国内外学者研究甚少。本工作旨在研究微缺陷对热喷涂涂层接触疲劳寿命及失效模式的影响。在接触疲劳实验基础上.建立了Weibull失效概率曲线图.比较了含有不同微缺陷涂层的接触疲劳寿命及主要的疲劳失效模式.为涂层的接触疲劳寿命预测提供了一条新思路。
1涂层制备及表征和接触疲劳实验
1. 1涂层制备
采用超音速等离子喷涂设备制备样品涂层.喷涂材料为NiCr13Si合金粉末.成分(质量分数/%.下同)为:C 0. 79,Cr 15. 8,13 3. 07,Si 4. 53,Fe 5.余下为Ni.基体选用调质45号钢圆环.内径、外径、高度分}!1为30,60,25mm.内、外孔处45。倒角.两端面及内孔均磨光处理。喷涂前用丙酮清洗基体表面.然后喷砂处理以提高基体表面粗糙度和表面活性。根据需要.在进行NiCr13Si材料的喷涂时.通过改变功率的大小和送粉量的大小来制备含不同微缺陷的涂层 ,喷涂工艺参数见表1。为防止基体过热.每喷涂约100pm后·暂停喷涂.使用压缩空气对基体进行冷却.喷涂过程重复进行5次。喷涂结束后.涂层厚度约为450-500pm。然后对涂层表面进行磨削处理.处理后涂层厚度约为350pm·表面粗糙度约为().2rcmo较大的孔隙这是由于空气的卷入形成的.较小的孔隙是由于熔滴的飞溅形成的。在送粉量较高.喷涂功率适中的情况下得到C.涂层.涂层层状结构不明显.无明显的微观裂纹.但孔隙率较高.并且孔隙尺寸较大.这是由于单位时间粉末喷射较多一些粉末会发生团聚.致使粉末颗粒变大.在撞击基体发生扁平化时.颗粒末熔化部分动量较大.直接被反弹.或被包裹到涂层中.导致空气卷入严重.形成较大的孔隙。
涂层内的微孔隙和微裂纹是构成涂层微缺陷的主体.喷涂功率和送粉量均对涂层的微缺陷有一定的影响。当喷涂功率较低时.涂层内的微孔隙和微裂纹含量较高.当送粉量较大时.涂层内的微孔隙含量较高.并且孔隙较大。基于涂层截面1000倍放大的SEM图像.采用灰度法测得涂层A , B , C的孔隙率分别为2.500.1.300.2.1000
1. 3接触疲劳寿命实验
采用YS-1型球盘式接触疲劳实验机.对涂层的抗接触疲劳性能进行测试。配对接触副为GCr15钢轴承球.直径为l lmm.表面粗糙度为0. 012pm·硬度为HRC60 0所有实验均在载荷为100N.转速为1500r/min的油润滑条件下完成。
每种涂层进行10次平行实验.以减少实验随机性带来的影响。接触疲劳实验结果如表2所不.其中:表面磨损失效表T为:SA(Surface Abrasion).剥落失效表T为:SPCSpalling).分层失效表T为:IDCInterfacialDelamination)。
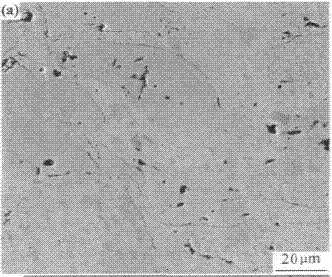 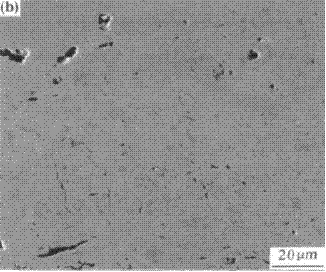 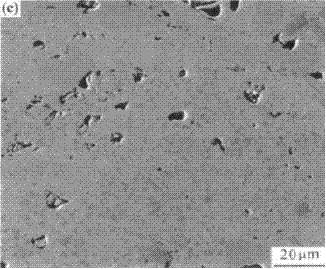
参考文献 略
本站文章未经允许不得转载;如欲转载请注明出处,北京桑尧科技开发有限公司网址:http://www.sunspraying.com/
|